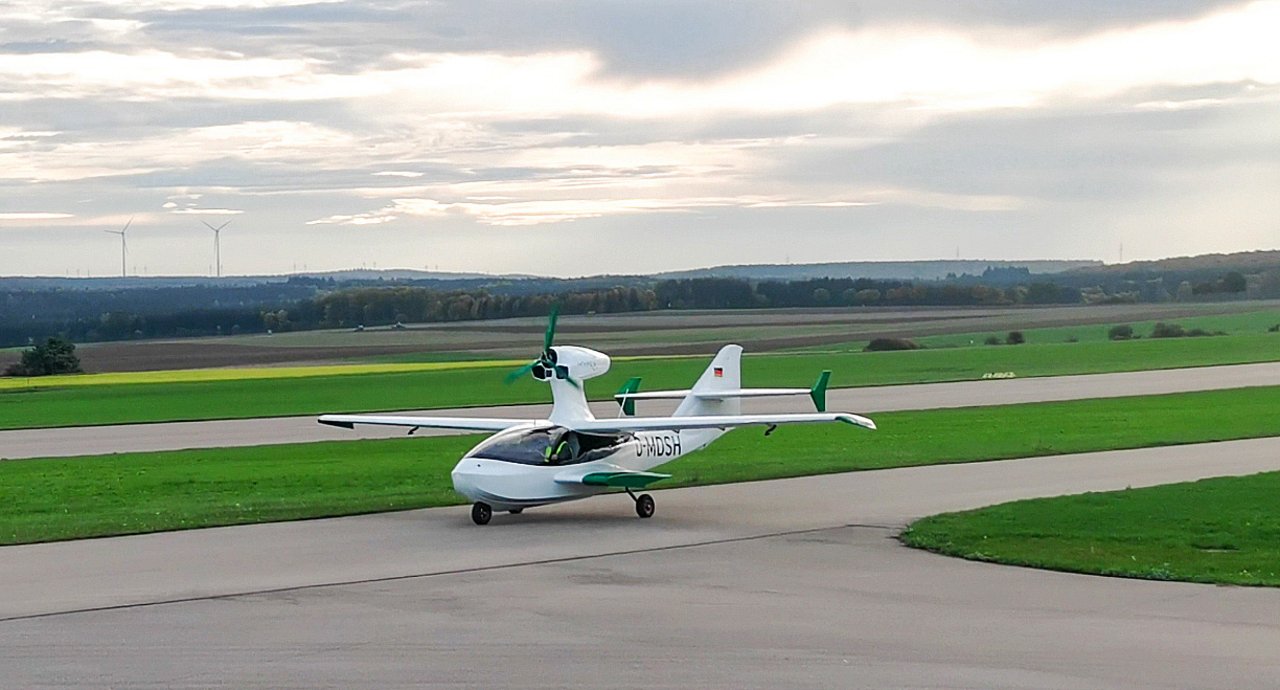
RAMPF-Epoxidharz beflügelt nachhaltige Luftfahrt
Der Erstflug des Brennstoffzellenantriebs HYFLY H167 war ein voller Erfolg. Mit an Bord des Testflugzeugs war das Hochleistungs-Epoxidharz RAKU® TOOL EI-2511/EH-2990 von RAMPF, das für die Herstellung des extrem leichten und robusten Gehäuses der Batteriebox eingesetzt wurde.
Kernaussagen
- RAMPF hat mit dem Engineering-Dienstleister Kasaero ein Hochleistungs-Batteriegehäuse für ein Leichtflugzeug mit Wasserstoff-Brennstoffzellenantrieb entwickelt und gefertigt.
- Die Lay-up-Werkzeugformen wurden anhand der CAD-Daten von Kasaero aus dem Epoxidboard RAKU® TOOL WB-0890 gefertigt.
- Das Epoxidharz RAKU® TOOL EI-2511/EH-2990 wurde zur Imprägnierung der finalen Bauteile auf der Form verwendet.
Drei Jahre intensiver Entwicklungsarbeit haben sich gelohnt: HYFLY, eine Kooperationsplattform für die Entwicklung nachhaltiger Ultraleicht- und Kleinflugzeuge, hat den ersten Testflug mit dem elektrischen Wasserstoff-Brennstoffzellenantrieb H167 auf dem Flugplatz Aalen-Heidenheim erfolgreich absolviert.
Die Brennstoffzelle, ausgestattet mit einem kugelförmigen Tank, der bis zu sieben Kilogramm Wasserstoff fasst, liefert eine Ausgangsleistung von 70 Kilowatt. Ziel ist, eine Flugdauer und Reichweite zu erreichen, die mit der eines konventionell angetriebenen Ultraleichtflugzeugs vergleichbar ist, wobei eine maximale Flugzeit von bis zu sieben Stunden angestrebt wird.
Das Gehäuse der Batteriebox des Testflugzeugs wurde von der Kasaero GmbH, einer führenden Entwicklerin von Hochleistungsflugzeugen und -komponenten mit Sitz in Stuttgart, aus Glasfaserverbundwerkstoffen entworfen. Der Rahmen und das Gehäuse sind so konstruiert, dass sie minimales Gewicht bei maximaler Festigkeit und Haltbarkeit bieten und somit höchsten mechanischen und thermischen Belastungen sowie Schwingungseinwirkungen standhalten.
Ultraschnelle Infusion mit RAKU® TOOL EI-2511/EH-2990 Epoxidharz
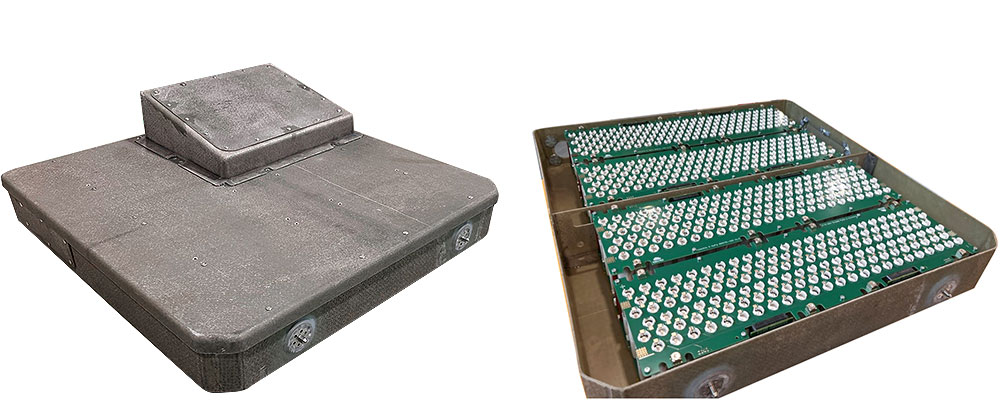
Die Composite-Teile wurden im VARTM-Verfahren (Vacuum Assisted Resin Transfer Molding) hergestellt. Die Formen für die Legewerkzeuge wurden direkt aus den CAD-Daten von Kasaero unter Verwendung des Epoxid-Blockmaterials RAKU® TOOL WB-0890 von RAMPF gefertigt.
Das WB-0890 überzeugt durch hervorragende Bearbeitbarkeit und Dimensionsstabilität sowie eine feine, glatte Oberfläche, welche die Nachbearbeitungszeit verkürzt und den Versiegelungsaufwand minimiert. Die Oberflächenbeschaffenheit der Masterform kann direkt auf die Prepreg-Form übertragen werden, wodurch das Nachschleifen entfällt und die Lebensdauer der Prepreg-Form erheblich verlängert wird.
Für die Imprägnierung der fertigen Teile auf der Form wurde das RAMPF-Epoxidharz RAKU® TOOL EI-2511/EH-2990 verwendet. Das flammhemmende Strukturharz mit hoher Tg (trocken 165 °C, nass 137 °C) erfüllt die Brandschutzanforderungen des 12- und 60-sekündigen vertikalen Beflammungstests sowie den Ölbrennertest für Brandschotte, Kompetenten für Triebwerksgondeln und Ladungsauskleidungen. Das Epoxidsystem weist eine niedrige Viskosität bei niedriger Verarbeitungstemperatur auf (200 mPas bei 40 °C).
Max Schultes, CTO bei RAMPF Composite Solutions:
RAKU® TOOL EI-2511/EH-2990 ermöglicht eine schnelle und unkomplizierte Bearbeitung ohne kostenintensive Infrastruktur. Selbst bei komplexen Bauteilen werden lediglich eine Vakuumpumpe und ein Ofen benötigt.
Schlüsselfertige Engineering-Lösungen für hochtechnische Composite-Teile
Auch die Endmontage des Batteriegehäuses wurde von RAMPF durchgeführt. Die Unternehmen der internationalen Gruppe kombinieren leistungsstarke Tooling-Materialien und Harzsysteme mit fundiertem Know-how in der Konstruktion und Fertigung von Verbundwerkstoffen:
- RAMPF Group, Inc. mit Sitz in Wixom, Michigan, USA, bietet kosteneffiziente Werkzeuglösungen und Vorrichtungen sowie leistungsstarke Strukturharze.
- RAMPF Composite Solutions mit Sitz in Burlington, Ontario, Kanada, ist auf Werkzeug- und Bauteildesign, Materialqualifikation, integrierte Qualitätssicherung sowie automatisierte Fertigungsprozesse für Komponenten und Subsysteme spezialisiert.
Max Schultes:
Das vielfältige Material- und Engineering-Portfolio von RAMPF ermöglicht die schnelle und effiziente Entwicklung hochtechnischer, skalierbarer Lösungen für zukunftsweisende Composite-Teile. Prototypen werden bereits innerhalb weniger Wochen nach der Konstruktion gefertigt, mit einer Kostenersparnis von bis zu 30 Prozent im Vergleich zu herkömmlichen Prepreg-Lösungen.
Projektfinanzierung durch ZIM und NRC
Das HYFLY-Projekt wird durch das Zentrale Innovationsprogramm Mittelstand (ZIM) des Bundesministeriums für Wirtschaft und Klimaschutz (BMWK) sowie dem National Research Council of Canada (NRC) gefördert. ZIM unterstützt innovative KMU, während der NRC als führende kanadische Forschungs- und Innovationsorganisation in Zusammenarbeit mit Industrie, Regierung und Wissenschaft Fortschritte in Bereichen wie Luft- und Raumfahrt, Gesundheit, Energie und Informationstechnologie vorantreibt.
Atefeh Nabavi, Director of Engineering & Quality bei RAMPF Composite Solutions:
Wir schätzen die großzügige Unterstützung von ZIM und NRC sehr. Diese war entscheidend, um dieses Projekt zu ermöglichen und den technologischen Fortschritt in der Luft- und Raumfahrt voranzutreiben.