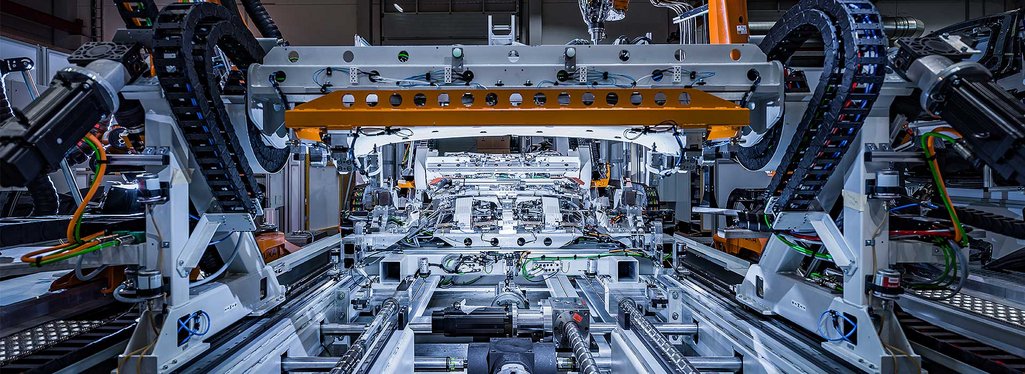
RAMPF und der neue ID.3 von Volkswagen – Eine Verbindung, die hält
Als Zulieferer für die Klebetechnik des neuen Elektromodells ziehen RAMPF Production Systems und Volkswagen an einem Strang.
Im September 2019 wurde er stolz auf der IAA in Frankfurt präsentiert, seit 2020 ist er auf dem Markt – der ID.3 von Volkswagen.
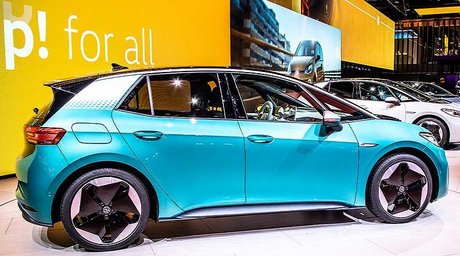
So futuristisch er vorne beginnt, so endet er am Heck – formvollendet.
Mit diesen treffenden Worten beschreibt VW sein erstes Kind der neuen ID-Familie und möchte mit ihm die Wende hin zur Elektromobilität einläuten. Viele Hoffnungen stecken in dem gut vier Meter langen reinen E-Modell, vor allem soll er die Elektromobilität massentauglich machen.
Vollautomatisierung ergänzt Fließbandfertigung
Für dieses ehrgeizige Ziel setzt der Konzern weitgehend auf die vollautomatisierte Fertigung in seinem Werk Zwickau, wo der neue ID.3 vom Band rollt. Etwa 1.500 Roboter in mehrstöckigen Fertigungslinien werden dort eingesetzt.
Sechs Roboter für diesen Fertigungsumfang stehen im Volkswagen Stammwerk in Wolfsburg und stammen vom Dosierspezialisten RAMPF Production Systems aus Zimmern ob Rottweil, wo drei vollautomatisierte Anlagen für die Fügung der Heckklappe des neuen ID.3 entwickelt und produziert wurden.
Als Experte in Sachen automatisierte Dosiertechnik ist RAMPF Production Systems bereits langjähriger Partner des VW-Konzerns. Doch die Anfrage nach zunächst zwei baugleichen Roboteranlagen, welche die vollautomatisierte Fügung der sportlichen Heckklappe samt Spoiler vornehmen sollen, forderte das RAMPF-Team heraus.
Die Größe der geplanten Anlagen: überdimensional. Die Technik: robotergestützte Vollautomatisierung in höchster Vollendung, so umfangreich und technisiert wie kein anderes RAMPF-Projekt bisher. Die Kundenansprüche: anspruchsvoll.
Zahlreiche Verhandlungen und Workshops später machten sich die zuständigen Projektleiter in Zimmern an die Planung und erarbeiteten gemeinsam mit Volkswagen ein innovatives Konzept.
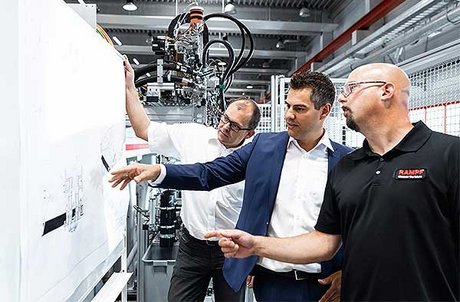
Teamwork und gesammeltes Technik-Know-How machen das Großprojekt möglich
Die Versuchsphase in der Anwendungstechnik wurde eingeleitet, ein geeignetes Serienwerkzeug entwickelt. Die Tüftler und Denker bei RAMPF arbeiteten wochenlang an einer idealen Klebelösung, welche die Heckklappe samt Spoiler untrennbar verbinden sollte.
Tests zur optimalen Oberflächenbehandlung von der Plasmavorbehandlung bis zur Beflammung nahmen viel Zeit und Ressourcen in Anspruch. Auf dem Weg zur idealen Lösung wurde ganz nebenbei sogar ein neues COD-Verfahren entwickelt (Curing on Demand = Aushärtebeschleunigung durch Wärme). Der dynamische und gleichzeitig auch robuste Beflammprozess durch einen Roboter und der Einsatz eines flexiblen Zwei-Komponentenklebstoffes erwies sich nach dem Durchschleusen zahlreicher Versuchsbauteile schließlich als die ideale Kombination, was auch die durchgeführten Zerreißproben bestätigten.
Man konnte Volkswagen schließlich stolz mitteilen: Heckklappe und Spoiler halten felsenfest. Nach sechs Monaten begann die Entwicklung der Gesamtanlage.
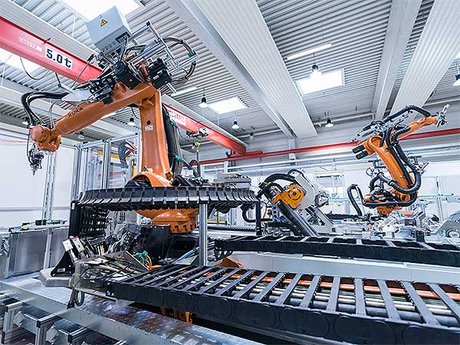
Auf dem Weg zur technischen Perfektion
Das erste Konzept mit mehreren aneinander gereihten Dosierzellen wurde jedoch schnell verworfen, viel großzügiger und vor allem automatisierter sollte die Fügung ablaufen. Auch die zunächst geplante Kettenförderung der Bauteile musste durch flexiblere Förderbänder ersetzt werden. Stolpersteine, die bei RAMPF für Kopfzerbrechen sorgten und das Projekt auf eine harte Probe stellten.
Doch die Techniker von Volkswagen und RAMPF bildeten trotz einiger Zweifel und Kompromisse ein perfektes Team und entwickelten zusammen ein extrem variables und großzügiges Achsenkonzept, das am Ende viel mehr automatisierte Bewegung in die Anlage brachte, als von VW zunächst vorgesehen.
Entstanden ist eine stattliche Dosieranlage mit fünf vollautomatisierten Fügewerkzeugen, zwei siebenachsigen hochdynamischen Robotern, umfangreichen Werkzeug-Achssystemen sowie einer aufwendigen Vor- und Nachbehandlung der Bauteile. Die Anlagensteuerung wurde in Zusammenarbeit mit KUKA speziell für die Anforderungen von Volkswagen entwickelt.
Komplette Vorserie in Zimmern gefügt
Für die Vorab-Produktion wurden sämtliche Heckklappen übrigens im Technikum des RAMPF-Werks in Zimmern geklebt, verpackt und verschickt. Abermals eine logistische Herausforderung, die das RAMPF Team jedoch mit Bravour meisterte, genauso wie den Abbau und erneuten Aufbau der ersten Anlage in Wolfsburg, der weitere neun Wochen in Anspruch nahm.
Kaum war diese in Betrieb, begann das RAMPF Team sofort mit der zweiten, baugleichen Anlage, welcher inzwischen noch eine dritte folgte. Der erfolgreichen Serienfertigung des neuen ID.3 steht zumindest für dessen Heckklappe nichts mehr im Wege, Teamwork und RAMPF Know-How sei Dank.
Das für RAMPF bislang größte Vollautomatisierungsprojekt nahm von der Projektierung bis zur fertigen dritten Anlage rund zwei Jahre in Anspruch. Eine Zeit mit Höhen und Tiefen, geprägt von vielen technischen Hindernissen, Meisterleistungen und erfolgreich erreichter Ziele. Denn trotz des sehr hohen Automatisierungsgrades wurde die von VW anvisierte Ausbringungsmenge abstimmungsgemäß eingehalten. Ein perfektes Ergebnis, das sowohl bei RAMPF als auch bei Volkswagen für Begeisterung sorgte.
Bei RAMPF ist man stolz, Teil einer zukunftsträchtigen Entwicklung zu sein und einen kleinen Beitrag zur umweltschonenden Elektromobilität geleistet zu haben. Und natürlich freut man sich über jeden ID.3, der mit untrennbar verklebter Heckklappe das Werk verlässt, formvollendet mit Know-How von RAMPF.