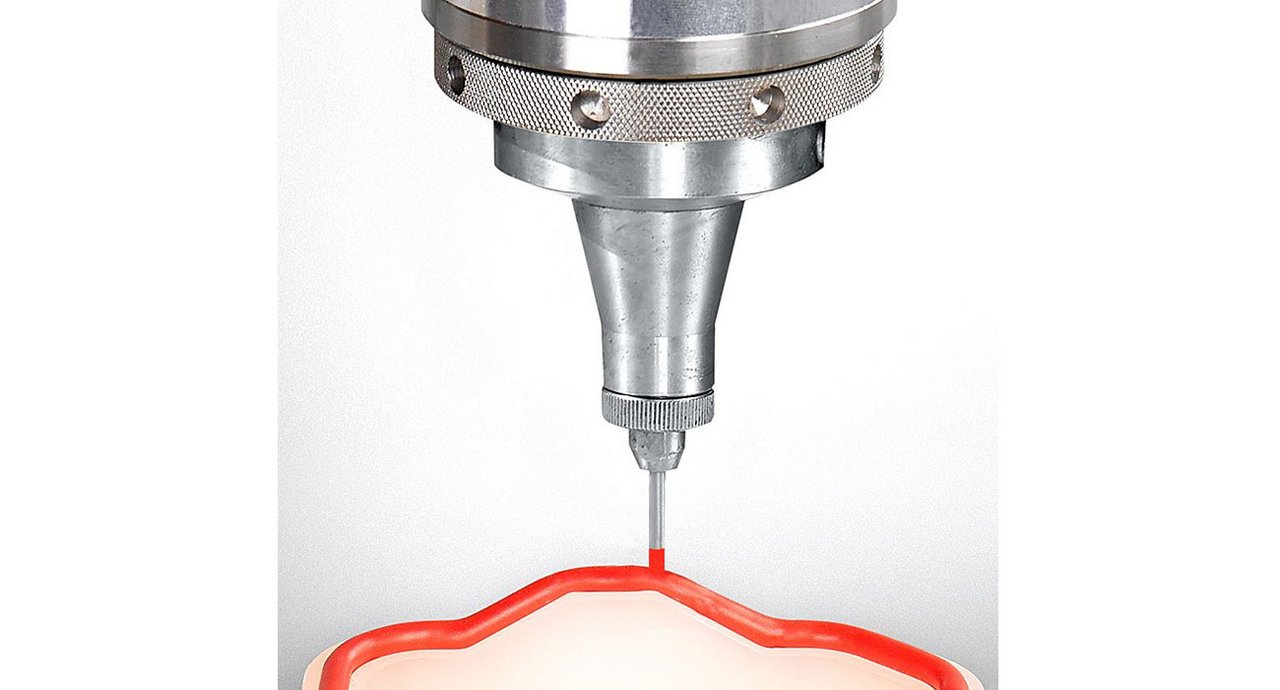
Dauerhafte Dichtigkeit im Automobil
Innovative Produktionssysteme mit integrierten Dosieranlagen für die Applikation von Polyurethan- und Silikonschäumen stehen im Fokus des Auftritts von RAMPF Production Systems auf der Fakuma 2017 – Halle B2, Stand 2203.
2K-In-situ-Dichtungen können dank innovativer Materialien und neuester Fertigungs- und Montageprozesse in immer mehr Anwendungen mit unterschiedlichsten Anforderungen und Dichtungsgeometrien eingesetzt werden. Dort sorgen sie für den sicheren und effizienten Schutz vor Feuchte und chemischen Einflüssen sowie diversen Umwelteinwirkungen.
Vor allem im Automobil- und Fahrzeugbau sind 2K-In-situ-Dichtungen allgegenwärtig: Tür- und Türschlossmodule, Lautsprecherboxen, Airbag-, Klimaanlage- und Handschuhfachabdeckungen, Bremslichter und Scheinwerfer, Heckleuchten, Elektrogehäuse, Zündspulenabdeckungen, Sicherungsboxen, Lüftungsgitter, Wasserkästen, um nur einige zu nennen.
Hierbei sind thixotrope Dichtungsschäume die am häufigsten eingesetzte Schaumart. Sie werden bei Anwendungen auf Fläche bei dreidimensionalen Bauteilen oder mit flacher Nut im Höhen-Breiten-Verhältnis von 1:2 bis zu 1:1 ohne Ablaufen / Tropfen des Materials appliziert. Es erfolgt kein übermäßiges Eindringen in offenporige Materialien (z. B. Textilien), was vor allem für den Einsatz im Fahrzeuginnenraum von Bedeutung ist.
Maximaler Kundennutzen durch Prozess- und Automatisierungskompetenz
Auf Anlagen von RAMPF Production Systems, einem führenden Anbieter von innovativen Produktionssystemen mit integrierten Dosieranlagen mit Sitz in Zimmern o. R., können alle handelsüblichen Polyurethan- und Silikonschäume zu Dichtungen verarbeitet werden. Diese werden mit mehrachsigen Robotern auf ebene und gekrümmte Flächen aufgetragen. Nach der Aushärtung haftet auf dem Bauteil eine stoßfreie Dichtung, die statisch gegen Staub, Feuchtigkeit und Nässe abdichtet. Die Dichtungen können auch formgebunden hergestellt werden.
Zusätzlich zur Kernkompetenz Misch- und Dosiertechnik werden projektspezifische Automatisierungskonzepte mit integriertem Teiletransport und Wärmebehandlung, Technologien der Montage- und Fügetechnik sowie logistische und qualitätssicherungsrelevante Lösungen angeboten. Sowohl die Integration von Oberflächenaktivierungsprozessen als auch Prüf- und Messtechnik zur Absicherung der Produktionsprozesse sind Teil der kundenspezifischen Lösungen.
„Durch die Verbindung von Prozesskompetenz und der passenden Automatisierungslösung sind wir in der Lage, unseren Kunden gesamtheitliche Lösungen für ihre Produktionen anzubieten“, so Hartmut Storz, Geschäftsführer von RAMPF Production Systems. „Unsere umfassenden Erfahrungen aus der erfolgreichen Umsetzung von über 2.800 Projekten weltweit gewährleistet, dass wir für jeden Kunden die beste Lösung finden – und das schnell und effizient.“