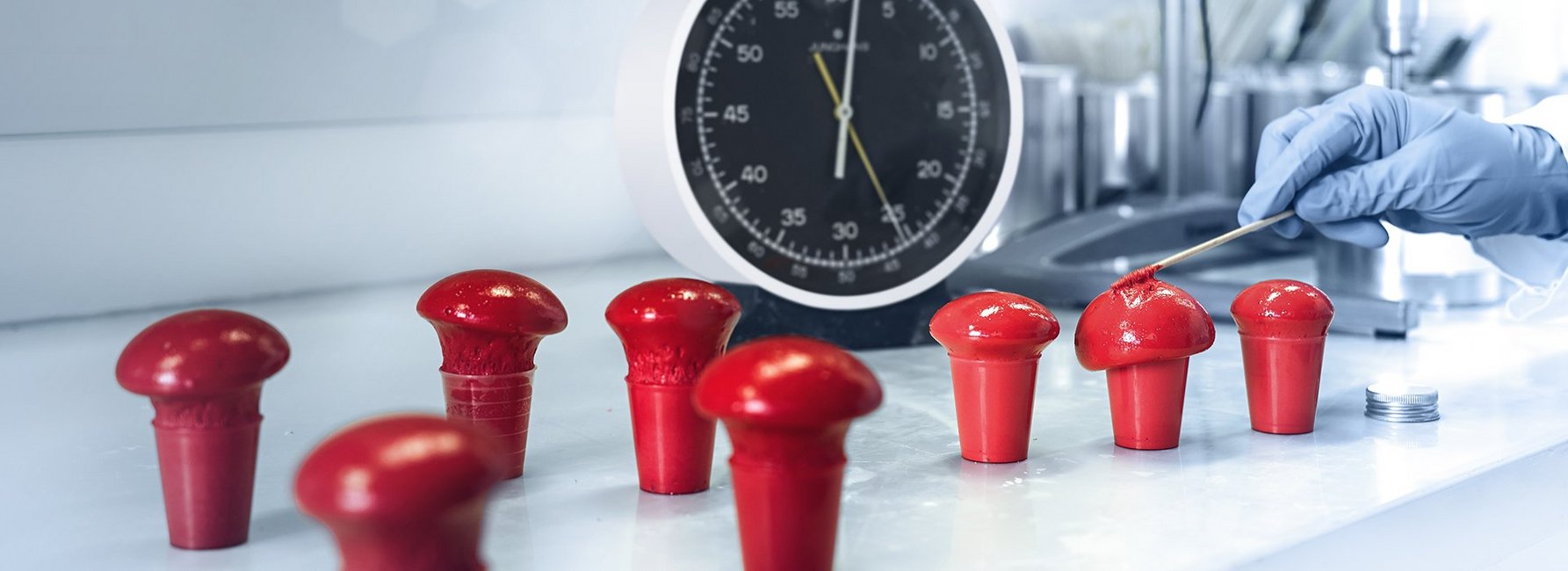
The all-rounders based on Polyurethane and Silicone
The basic task of sealing systems is to efficiently protect components against moisture, chemicals, and various environmental influences.
RAMPF Advanced Polymers is a leading specialist in liquid to highly thixotropic two-component foam gaskets and elastomer seals based on polyurethane and silicone.
The foam gaskets are processed using FIPFG (formed in place foam gasket) or FIPG (formed in place gasket) technology.
The advantage: Unlike inserted or stuck-on seals, our sealing systems are applied directly on the component by dispensing machines. They expand in situ and bond very quickly, which reduces cycle times and also ensures more efficient processing.
Our RAKU® PUR and RAKU® SIL systems combine efficient sealing with the highest quality and exceptionally easy handling.
By developing new products and optimizing existing ones, RAMPF Advanced Polymers ensures the toughest demands in terms of seal quality, sealing geometries, and mechanical, thermal, and chemical resilience are always met.
What’s more, processing properties such as reactivity, viscosity, and color can be tailored to customer requirements.
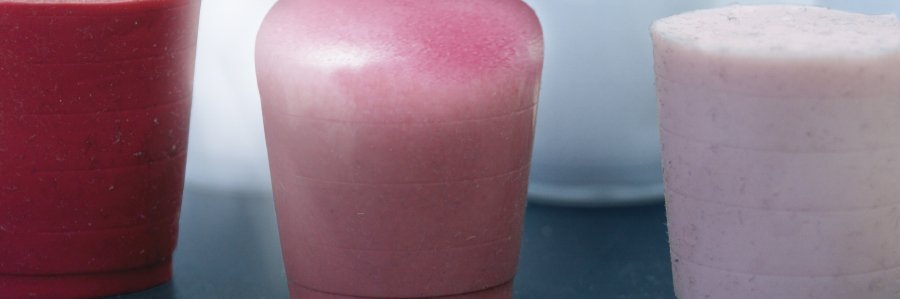
Your key benefits
- Many years of experience in product development and processing technology
- IATF 16949 and ISO 14001 certification
- Used by leading manufacturers for both indoor and outdoor applications, including in the automotive and electronics industries
- Reduced noise and vibration
- Perfect sealing thanks to automatic application of the liquid gasket
- Economic benefits thanks to accelerated and simplified production and assembly processes
- Reliable and lasting tightness – the gasket is firmly attached to the component and cannot be removed
- No tool costs; flexible adaptation to modified components using NC technology
Material types for sealing systems – polyurethane or silicone?
Choosing the most suitable sealing material is a decision based on
Area of application
Customer-specific chemical requirements
Processing procedure
Area of application
- Temperature resistance, long-term: from -40 to +100°C; short-term: +140°C
- Chemical resistance to fats and oils, detergents, aqueous solutions, etc.
Properties
- Outstanding physical properties such as compression set, tensile strength, elongation at break, etc.
- Low water absorption
- UV-resistant formulations possible
Area of application
- Temperature resistance, long-term: from -60 to +200 °C; short-term: +300 °C
- Exceptional chemical resistance for extreme environments
Properties
- Optimum physical properties such as compression set across the entire application temperature range
- Extremely water-repellent
- Excellent UV resistance