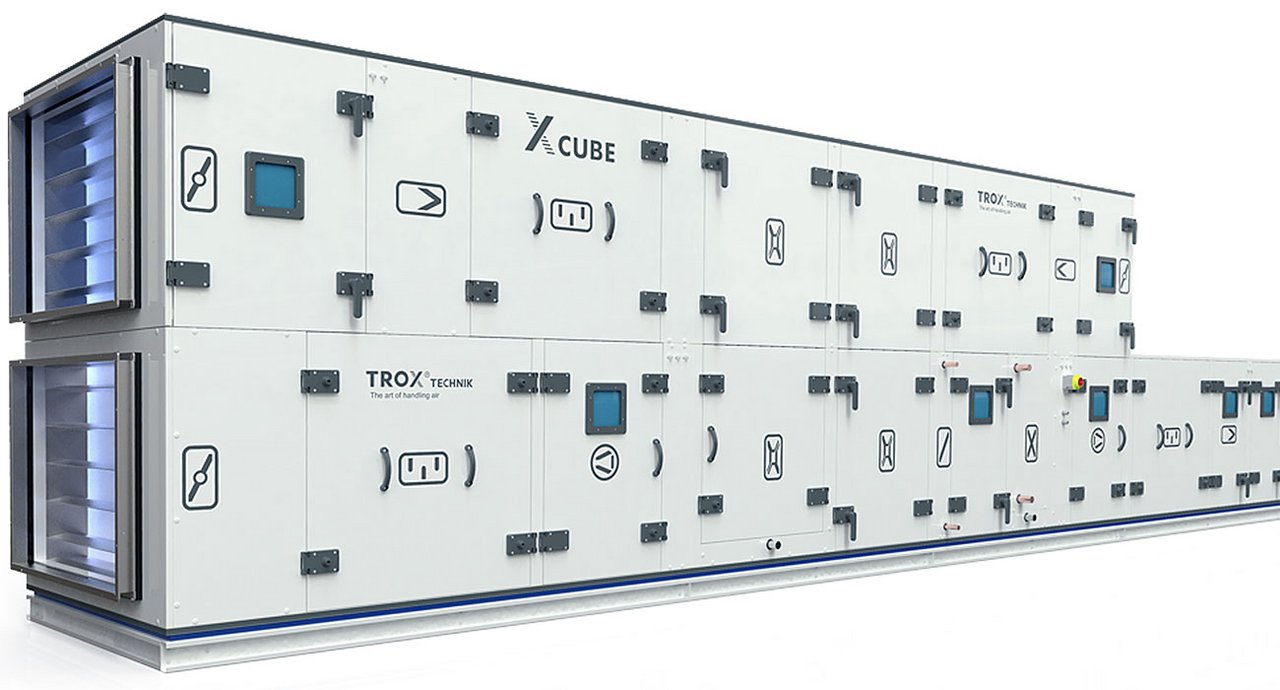
Clean Air Thanks to TROX and RAMPF
TROX GmbH is a global leader in the development and manufacture of components, appliances, and systems for indoor air conditioning and ventilation. Based in Neukirchen-Vluyn, Germany, the company uses antibacterial polyurethane systems from RAMPF Polymer Solutions to seal, cast, and bond its air filters.
Even before the coronavirus pandemic hit, the importance of clean air was well known. In operating rooms and intensive care units, lives depend on good air quality. It is also a critical production factor in the pharmaceutical, aerospace, and semiconductor industries.
The pandemic did, of course, highlight the importance of effective ventilation systems, including for schools, offices, restaurants, theaters, and exhibition centers. With its comprehensive portfolio of ventilation and air-conditioning systems, TROX provides a tailored solution for each of these challenges.
Pascal Pollmann, Product Manager Filter Technology at TROX GmbH:
In order to find new materials that meet our requirements, we were looking for a supplier with an innovative approach and high-quality products. RAMPF Polymer Solutions fitted the bill perfectly and has enabled us to improve our products.
Antibacterial polyurethane systems for filter production
TROX uses antibacterial polyurethane sealing and casting systems from RAMPF Polymer Solutions for the production of air filter elements:
- Rigid foam: A RAKU® PUR two-component rigid foam is used to seal filter elements. Exhibiting excellent mechanical properties, its rapid curing also results in very short process times.
- Casting materials: RAKU® PUR two-component casting materials secure the individual filter elements in the filter frame. Ensuring maximum stability, the systems also benefit from high mechanical strength and outstanding adhesive properties.
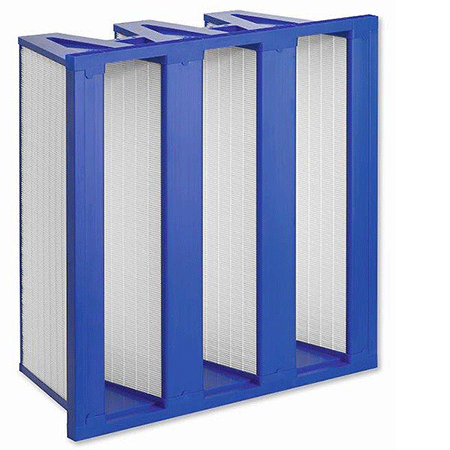
Two-component adhesive for the X-CUBE X2 series of air handling units
TROX is using a RAKU® PUR two-component adhesive to manufacture its new X-CUBE X2 series of air handling units (picture top of page). The bonding system that joins the individual components of the sandwich panels impresses with its short curing time, exceptional mechanical strength, and high temperature and chemical resistance.
Material and machine from a single source
The DR-CNC dispensing robot from RAMPF Production Systems is used to process the RAMPF Polymer Solutions rigid foam system for sealing the filter elements. Stand-out features include highly adaptable X-Y-Z axis strokes and state-of-the-art control technology that combines the mixing and dispensing system perfectly with the maintenance-free CNC linear axes.
The result is flawless interplay between the dispensing process and motion sequences.
Close collaboration between the two RAMPF companies and TROX means material and machine are ideally matched, which optimizes quality and minimizes process times.
Michael Wahl, Director Business Center Casting Resins & Elastomers at RAMPF Polymer Solutions:
We are delighted about our successful collaboration with TROX. Our open and trusting relationship ensures the development of high-performance polyurethane systems that are tailored perfectly to the relevant application requirements. Thanks to our highly qualified development team and modern laboratory, we can also offer TROX a high level of flexibility to make the development and production process even faster.