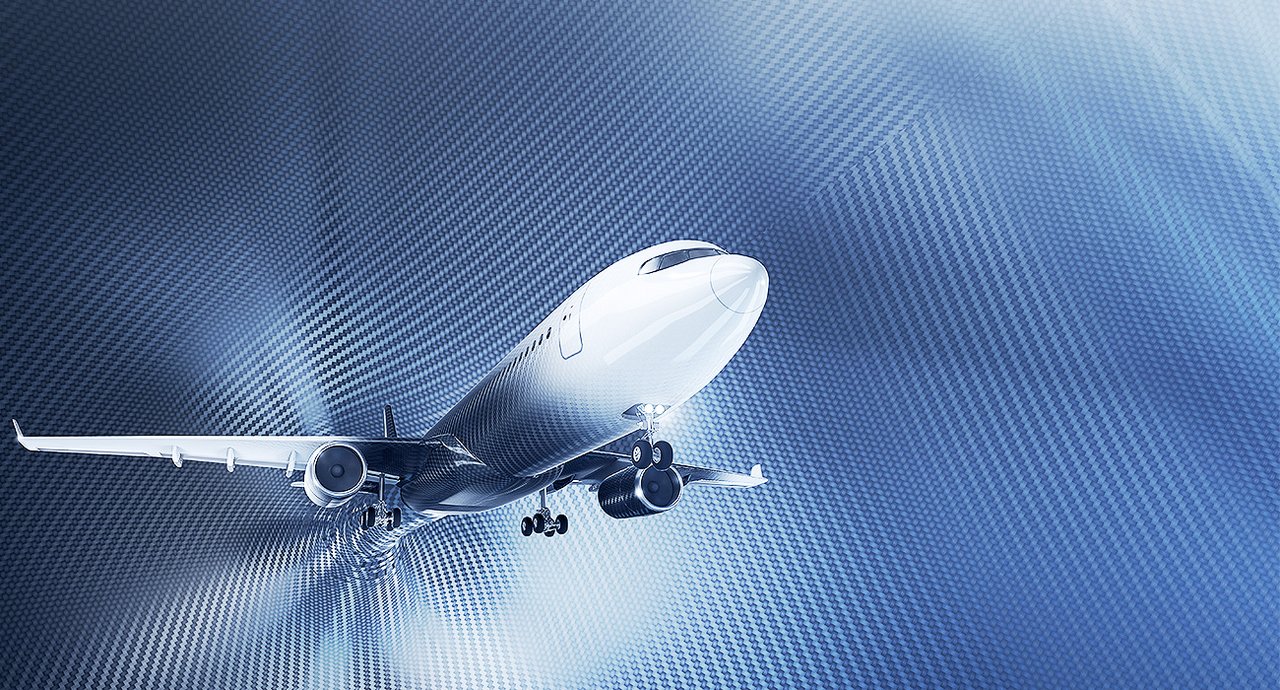
Quicker Time-to-Market at Lower Costs – Composite Manufacturing by RAMPF
RAMPF Composite Solutions is presenting one-stop engineered solutions for technologically advanced composite manufacturing for the aerospace and defense industries at Farnborough International Airshow in England from July 22 to 26 – Booth 4520.
Key facts
- RAMPF Composite Solutions increases speed-to-market and cost-efficiency of complex composite manufacturing.
- One-shot solution enables the manufacture of prototypes within a few weeks of design stage and with 25-30 percent cost savings.
- State-of-the-art, 74,000 square feet facility optimizes every stage of the composite manufacturing process.
RAMPF Composite Solutions designs and manufactures some of the world’s most complex lightweight composite products. The full potential of composite technology is utilized for both low-volume production / early product development and series production by combining:
- Low-cost tooling and fixtures with outstanding mechanical properties
- High-performance structural resins for effective and fast infusion
- Structural optimization via Tailored Fiber Placement (TFP) technology for maximum speed and accuracy
- Low-cost component production using Vacuum Assisted Resin Transfer Molding (VARTM)
The company’s groundbreaking, quick-turn solutions include material qualification, built-in quality assurance, and automated processes for the manufacture of components and subsystems.
RAMPF Composite Solutions can provide prototypes within weeks of the design stage and with 25-30 percent cost savings over more traditional prepreg solutions.
The benefits are maximized for components that exhibit high structural, geometrical complexity (undercuts, compound curvatures, pockets, etc.) and functional complexity (EMI shielding, static discharge, impact, flammability compliance).
RAMPF Composite Solutions’ state-of-the-art, 74,000 square feet facility in Burlington, Ontario, Canada, is designed to optimize every stage of the composite manufacturing process.
Facility features include:
- Temperature-controlled lamination room
- AI-optimized automated digital ply cutting system
- Automated metering, mixing, and dispensing equipment for a variety of resin systems
- Three large curing ovens
- Eight-head TFP machine
- Dual 5-axis CNC machines
- Dual paint booths and mixing kitchen
- Metallic plating capabilities
- Centralized vacuum pump system
- Robotic sanding equipment
- Ultrasonic non-destructive testing equipment
- Industrial 3D printer capable of thermoplastic printing
Larry Fitzgerald, CEO of RAMPF Composite Solutions:
Composites are the cornerstone of modern aerospace and defense innovation, providing unmatched strength-to-weight ratios, superior fatigue resistance, and transformative design flexibility. We have the engineering and production expertise as well as the necessary infrastructure to tackle the most demanding composite challenges. We look forward to showcasing our innovative solutions to global aviation leaders at Farnborough International Airshow.