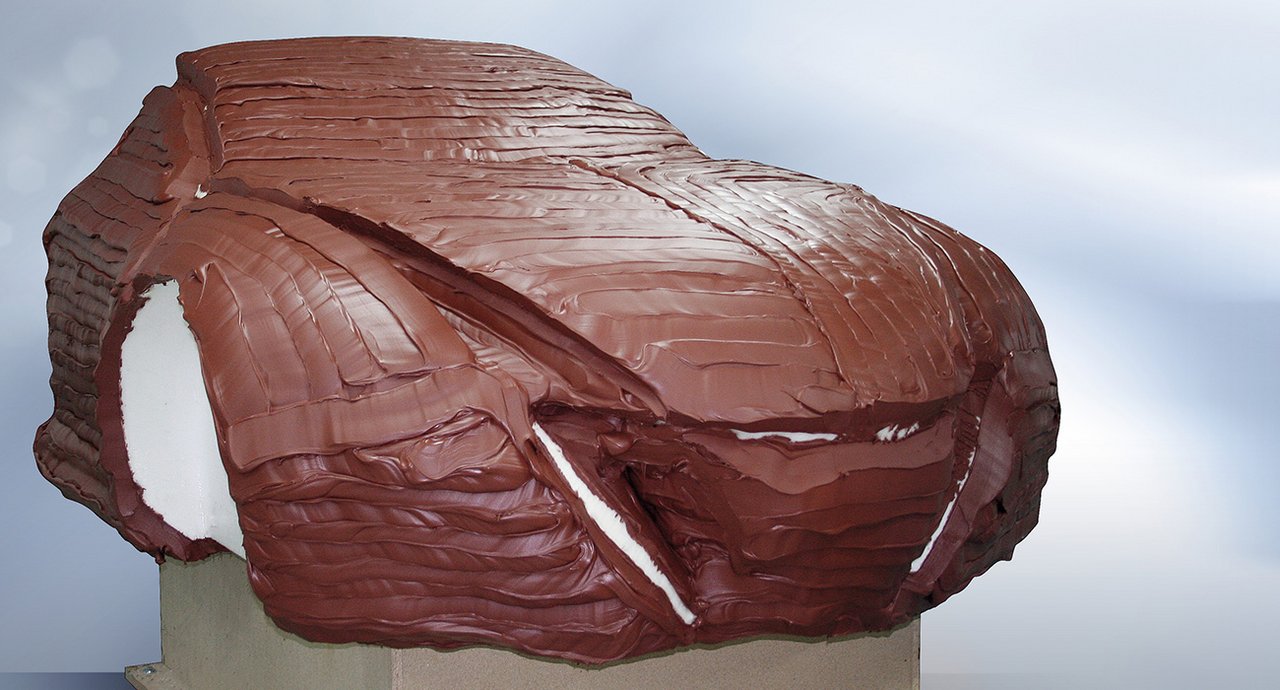
High-Quality and Low-Cost Tooling – RAMPF Close Contour Materials
Maximum speed and quality, minimum cost and waste – RAMPF Group, Inc. is presenting its Close Contour paste and casting portfolio for the production of models and molds at SAMPE 2024 in Long Beach, CA, from May 21 to 23 – Booth D26. A further highlight – Holistic engineered solutions for technologically advanced composite manufacturing by RAMPF Composite Solutions.
Key Facts
- 1. RAMPF’s Close Contour technology facilitates the fast, resource-saving, and waste-minimizing manufacture of high-quality models and molds.
- 2. RAMPF Group, Inc. offers a paste application service at the customer’s location.
- 3. RAMPF Composite Solutions increases speed-to-market and cost-efficiency of complex composite manufacturing.
Close Contour technology by RAMPF Group. Inc.
RAKU® TOOL Close Contour pastes and castings based on epoxy and polyurethane are used to manufacture high-quality models and molds that are already close to the shape of the final part. The benefits:
- Minimal material usage
- Minimal production waste
- Extremely fast milling
- First-class, seamless, and very fine surfaces without bonding lines
Close Contour Pastes
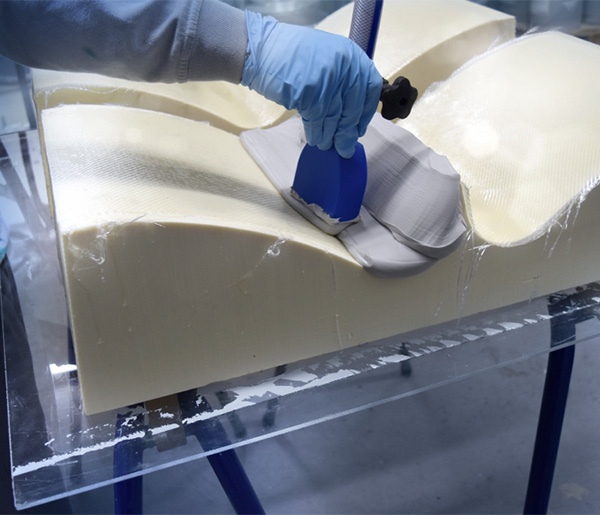
The two-component, thixotropic epoxy systems are applied to a close-contour shape supporting structure with a mixing and dispensing machine, cured, and then CNC machined according to customer CAD data; almost any kind of supporting structure can be used, including RAKU® TOOL SB-0080 styling board, EPS, and cast aluminum.
RAKU® TOOL Close Contour pastes exhibit outstanding dimensional stability and enable quick and easy processing with no slump on vertical surfaces and smooth overhead dispensing. Applications include design and styling models, molds, large-scale modeling, rotor blade, wind turbine, and boat models. RAMPF offers a paste application service and the comprehensive technical support of experienced engineers.
Close Contour Castings
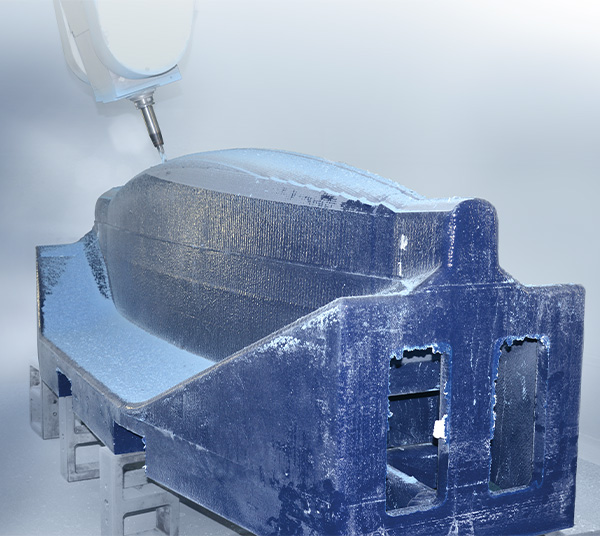
The semi-finished polyurethane systems are supplied as a three-dimensional casting. The monolithic, close-contour block with even wall thickness is manufactured by RAMPF in Southern California and North Carolina based on customer CAD data.
The cavity is milled into a lightweight mold material such as EPS or RAKU® TOOL SB-0080 styling board. Following the application of the release agent, the cavity is filled using a special casting process. Milling is quick and easy. Applications include styling, design, master, cubing, and data control models.
Cost-efficient and ultra-fast composite manufacturing by RAMPF Composite Solutions
Quicker time-to-market at lower costs – RAMPF Composite Solutions is presenting its holistic engineered solutions for technologically advanced composite manufacturing for the aerospace, defense, industrial, medical, high-end consumer, and green transportation industries.
The company utilizes the full potential of composites manufacturing for both low-volume production / early product development and series production by combining
- Low-cost tooling and fixtures
- High-performance structural resins
- Structural optimization via Tailored Fiber Placement (TFP) technology
Together with material qualification, built-in quality assurance, and automation processes, subsystems and fully scalable prototypes are manufactured within days or weeks of design stage via an innovative one-shot solution.
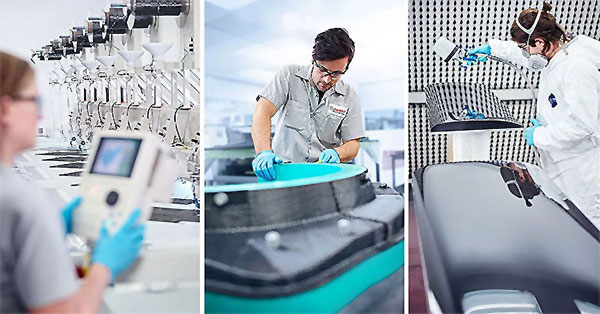