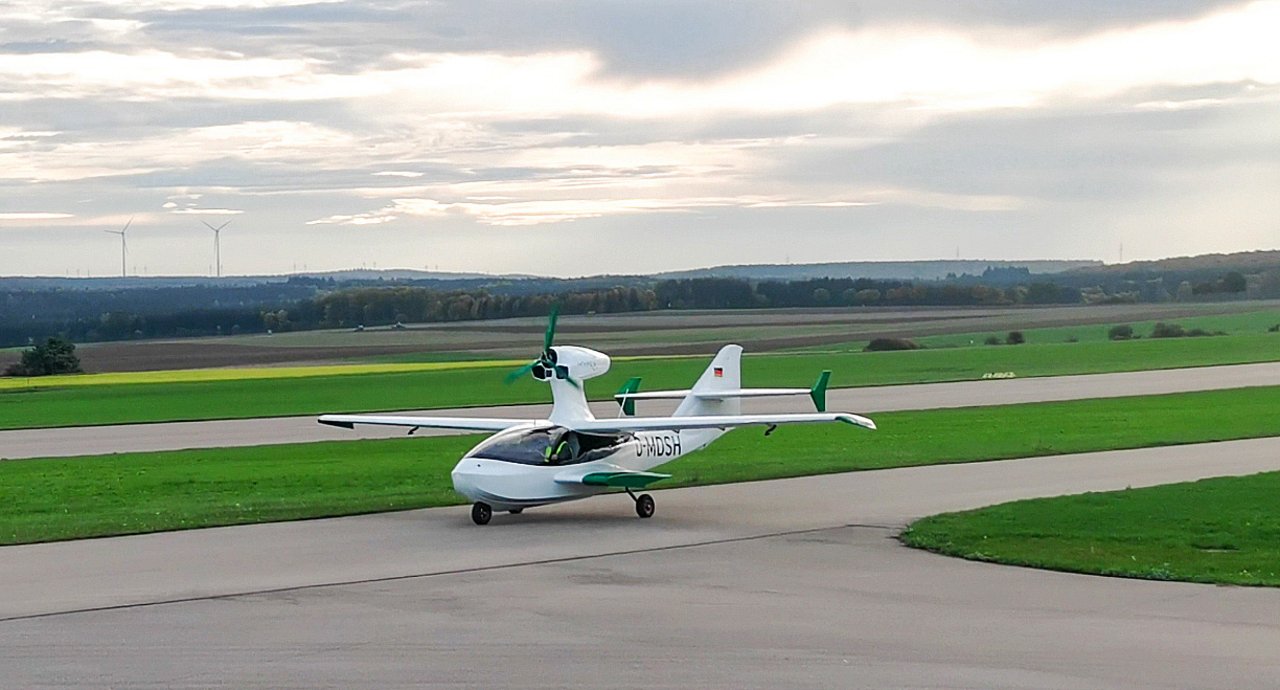
High-Performance RAMPF Epoxy Resin Powers Aviation Milestone
The maiden flight of the HYFLY H167 hydrogen fuel cell propulsion system was a full success. Aboard the test aircraft was RAMPF’s high-performance epoxy resin RAKU® TOOL EI-2511/EH-2990, which was used to manufacture the extremely lightweight and robust battery box housing.
Key Facts
- RAMPF has partnered with the engineering provider Kasaero to develop and manufacture a high-performance battery box housing for a lightweight aircraft with a hydrogen fuel cell propulsion system.
- The molds for the lay-up tools were directly manufactured from Kasaero’s CAD data using RAMPF’s RAKU® TOOL WB-0890 epoxy board.
- RAMPF’s epoxy resin RAKU® TOOL EI-2511/EH-2990 was used to impregnate the final parts on the mold.
Three years of intensive development work have paid – and taken – off: HYFLY, a collaborative platform for the development of sustainable powered motor gliders, ultralight and small aircraft, has successfully completed the first test flight with its H167 electric hydrogen fuel cell propulsion system at Aalen-Heidenheim airfield in southern Germany.
The fuel cell with a spherical tank capable of holding seven kilograms of hydrogen provides an initial power output of 70 kilowatts. The goal is to achieve flight duration and range comparable to that of a conventionally powered ultralight aircraft, with a maximum flight time of up to seven hours.
The housing of the test aircraft’s battery box was made from glass fiber composite and designed by Kasaero GmbH, a leading developer of high-performance aircraft and aircraft components based in Stuttgart, Germany. The housing’s frame and cover are engineered for minimal weight, maximum strength and durability, ensuring they can withstand highest mechanical, thermal, and vibrational loading.
Ultrafast resin infusion with RAKU® TOOL EI-2511/EH-2990 epoxy resin
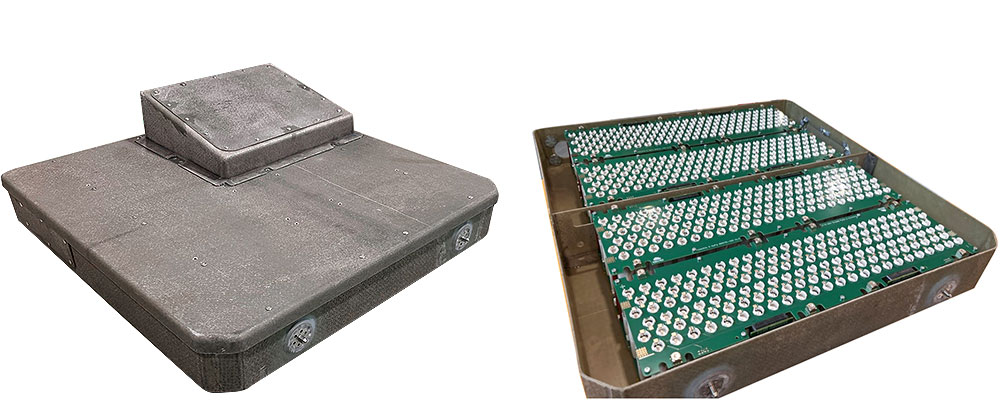
The composite parts were produced via Vacuum Assisted Resin Transfer Molding (VARTM). The molds for the lay-up tools were directly manufactured from Kasaero’s CAD data using RAMPF’s RAKU® TOOL WB-0890 epoxy board.
With excellent machinability and dimensional stability, the WB-0890 features a fine, smooth surface that reduces finishing time and minimizes the amount of sealer required. The master mold’s surface finish can directly be used a tool surface, enabling an excellent surface finish on the part.
RAMPF’s epoxy resin RAKU® TOOL EI-2511/EH-2990 was used to impregnate the final parts on the mold. The flame-retardant structural resin has a high Tg (dry 165 °C, wet 137 °C), exhibits low viscosity at low processing temperature (200 mPas at 40 °C), and fulfills 12 and 60 sec vertical burn tests as well as the oil burner test for firewalls, engine nacelle components, and cargo liners.
Max Schultes, CTO at RAMPF Composite Solutions:
RAKU® TOOL EI-2511/EH-2990 is processed easily and quickly without expensive infrastructure, only a vacuum pump and an oven are needed, even for complex structural components.
One-stop engineered solutions for composite manufacturing
RAMPF also completed the final assembly of the battery box housing, as the international group of companies combines high-performance tooling materials and resin systems with composite design, engineering, and manufacturing know-how:
- RAMPF Group, Inc. based in Wixom, MI, USA, provides cost-effective tooling / fixtures and high-performance structural resins.
- RAMPF Composite Solutions, located in Burlington, Ontario, Canada, specializes in tool and part design, material qualification, integrated quality assurance, and automated manufacturing processes for components and subsystems.
Max Schultes:
RAMPF’s comprehensive material and engineering portfolio allows us to deliver high-quality, scalable solutions for advanced lightweight composites quickly and efficiently. Prototypes are manufactured within weeks of the design stage and with up to 30 percent cost savings compared to more traditional prepreg solutions.
Project funding by ZIM and NRC
The HYFLY project is funded by the ZIM, an innovation program for SMEs launched by the German Federal Ministry for Economic Affairs and Climate Action (BMWK), and the National Research Council of Canada (NRC), the country’s premier organization for research and innovation that collaborates with industry, government, and academia to drive innovation in areas such as aerospace, health, energy, and information technology.
Atefeh Nabavi, Director of Engineering & Quality at RAMPF Composite Solutions:
We deeply appreciate the generous support of ZIM and NRC. This has been instrumental in enabling this work and driving groundbreaking advancements in technology that will shape the future of aerospace.