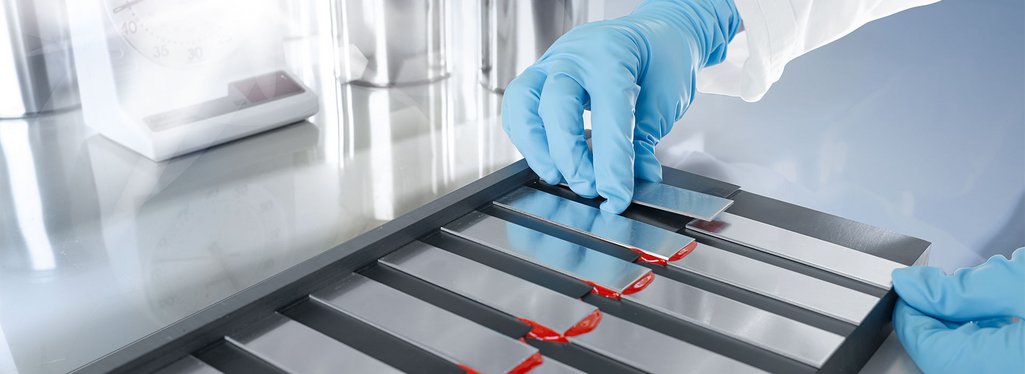
Bonding with hybrid adhesives
Vibrations, shocks, temperature fluctuations: bonded components are exposed to numerous stresses. That is why hybrid adhesives are used more and more often – including one-component systems from RAMPF Polymer Solutions.
Welding, soldering, screwing, riveting, and bonding – all these activities belong to the production technology of joining, the permanent connection of two components. Bonding is one of the oldest cultural techniques of mankind. It can be assumed that thousands of years ago, early humans already made use of the properties of “sticky” materials.
It was not until the development of synthetic adhesives in the 20th century that adhesive bonding established itself in industrial production. Over the years, bonding has developed into a key technology of the 21st century, due to the numerous advantages it brings.
The best of both worlds
Hybrid adhesives combine the characteristic properties of polyurethanes with those of silicones, thereby generating significant advantages over conventional systems. In addition to strength, one of the main criteria of any adhesive system, the current trend in the industry are adhesive bonds that combine strength and elasticity. This is particularly important when the bonded component is exposed to vibrations, shocks, or changing thermal loads.
Here in particular, hybrid systems offer an unbeatable combination of strength and flexibility.
The advantages of hybrid technology
The main advantages of hybrid adhesives are their strength and flexibility, which facilitates elastic bonding and compensates any expansion of the bonded components. Moreover, unlike pure polyurethane systems, hybrid adhesives are free of isocyanates. This means that they are not subject to classification according to the German Ordinance on Hazardous Substances and promote health and occupational safety.
In addition, hybrid adhesives can be used on a variety of material surfaces, often without pre-treatment. This also makes it possible to bond difficult substrates with simpler and therefore more cost-effective process control.
Hybrid adhesives are also silicone-free, which simplifies integration into existing production processes.
Dr. Christian Weber, Director of R&D at RAMPF Polymer Solutions:
The optimal combination of strength and flexibility makes the hybrid adhesive of the RAKU®SEAL brand a powerful addition to our existing product portfolio.