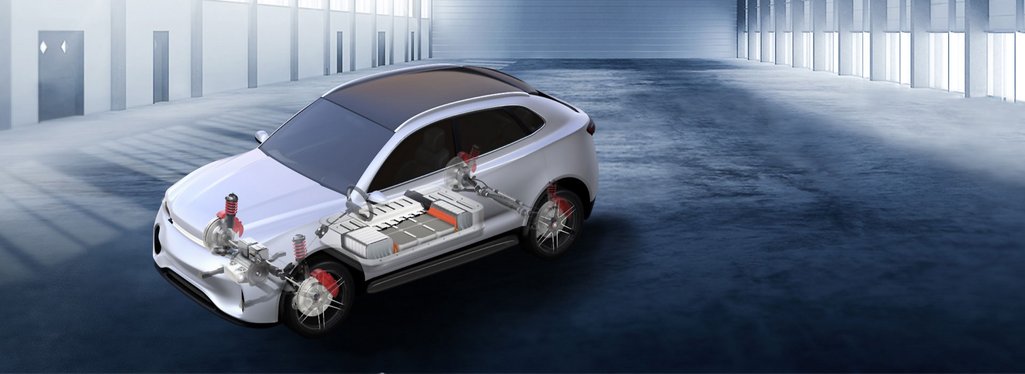
Mind the Gap
Electrical/electronic components produce heat – but must not overheat. This technical balancing act is accomplished by thermal management.
Stay Cool with Gap Fillers
While computers are cooled by circulating air, this is not possible in electro mobility applications due to the high component density. Here, thermally conductive pastes, so-called gap fillers, play the role of “heat manager”.
When cooling without air, the heated components are brought in contact with special heat sinks to dissipate the resulting heat. However, this usually results in very small air pockets, which considerably impede this dissipation of heat. This is due to the poor thermal conductivity of stagnant air, which is only 0.026 W/mk (watts per meter-kelvin).
By comparison, aluminum has a thermal conductivity of just under 250 W/mk.
To ensure efficient heat dissipation, the air gaps between the components and the heat-dissipating surface are sealed by gap fillers.
Paste > Pad
Gap fillers can be applied in different ways. On the one hand, there are gap filler pads that adapt to the surface of the electrical/electronic components and thus prevent air pockets. However, these pads are difficult to apply and can thus only be used in batch production.
Gap fillers made of silicone elastomers are more widespread and also part of the product portfolio of RAMPF. These are applied directly to the components with a dispensing system and therefore suitable for series production. The silicone paste cures under room temperature within about one hour, achieving a thermal conductivity of 1.8 - 4.5 W/mk.
The key benefit of the paste is that it can be applied individually according to the surface shape of the components; in contrast to the pads, there is no risk of using the wrong shape or size.
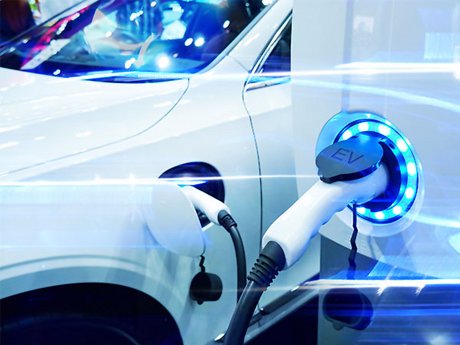
Gap-Filler: Enabler of Electric Mobility
In order to comply with the German government's ambitious climate goals in the transport sector, German car manufacturers are currently driving ahead the transition to electro mobility at full speed.
The discussed bans on diesel and gasoline engines from 2030 illustrate the urgency of this change.
The battery will take center stage in the cars of the future, and here thermal management will also be crucial.
The operating temperature of the battery pack has a decisive influence on the service life, safety, and capacity of the battery cells used.
Jihad Marzouki, Junior Key Technology Manager at RAMPF Polymer Solutions:
As a high-performance 'heat manager' our RAKU® SIL gap fillers are making an important contribution to the success of electro mobility.