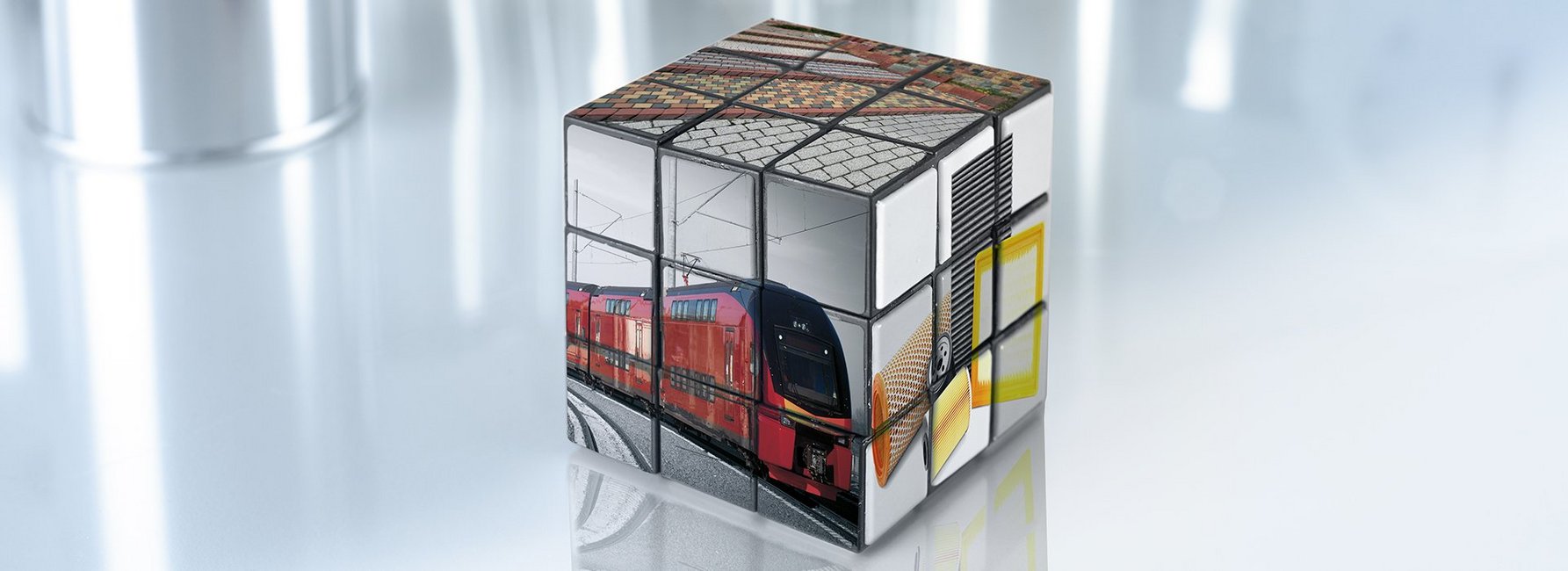
Highly Resilient Elastomers and Engineering Casting Resins
Core competencies of Casting Resins & Elastomers mainly consist of reactive casting systems based on 2K- polyurethane and 2K-epoxy systems as well as on cold cured elastomers.
Our RAKU® PUR (polyurethane), RAKU® POX (epoxy), and RAKU® SIL (silicone) systems can be individually adapted to your processes and requirements and are used worldwide in a wide variety of applications, especially
- Filters (casting, sealing air, oil, and hydraulic filters)
- Insulating panels (gelcoat layer and foam) for refrigerated vehicles
- Window frame bonding
- Edge casting for laboratory equipment, hospitals, and schools
- Elastomer molds for the cement industry
- Abrasives
Our diversity in this field means we are much in demand as a solution partner. We tailor our product development to your specific requirements regarding both the product and the processing procedure.
Together with application expert RAMPF Production Systems, we develop products that are used on the simplest manual mixing and dispensing systems to highly automated dispensing technology.
Material, machine, process – benefit from RAMPF’s highly competent complete service.