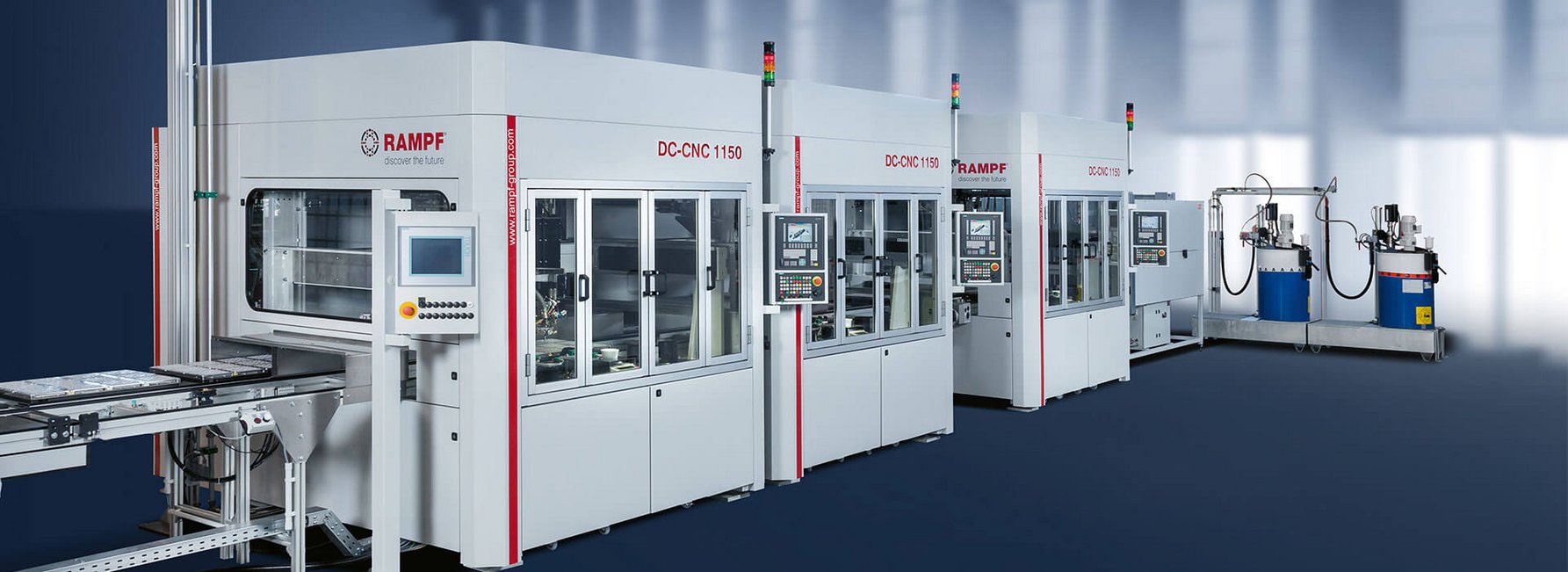
Sealing, Casting and Bonding of up to four components
Dispensing Systems & Robots
Every production process places unique requirements on the components of a dispensing system. For the best dispensing results, it is vital that material transport and preparation, dispensing, mixing technology, and moving axes are perfectly aligned.
We offer you dispensing systems that will ensure your current and future development. We develop complete, tailored solutions for reliable sealing, casting, and bonding of single- and multi-component materials.
Embedded in compact dispensing cells or dispensing robots, RAMPF dispensing systems form the perfect basis for production or integration into production systems.
Combined with high-performance controllers from SIEMENS or Beckhoff, our dispensing systems meet every requirement in terms of dynamism, interaction, and data management.
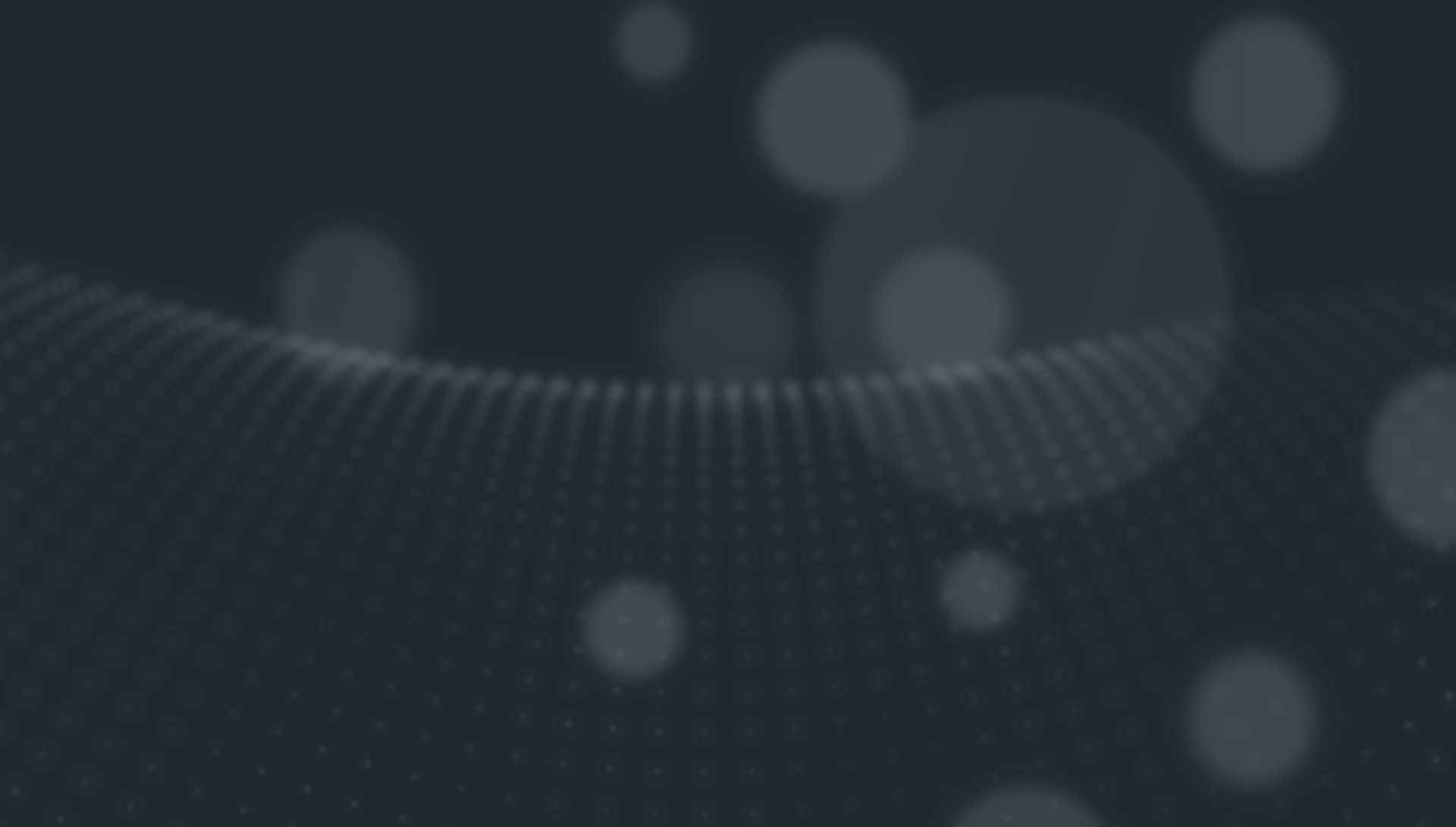
High-precision dispensing of single- and multi-component materials
We offer exceptionally powerful low-maintenance systems for high-precision dispensing of materials as varied as polyurethane, epoxy, and silicone, independent of fillers and viscosities.
Ultra-precise mixing
We offer you exceptionally powerful low-maintenance mixing systems. We also develop solutions for processing fast-sedimenting, highly abrasive, and highly viscous materials to suit your specific requirements.
The tried-and-tested basic mixing system has been used thousands of times in industrial applications. Materials are dispensed to the mixing chamber via pneumatically actuated needle seat valves. The mixing chamber and mixer are made of stainless steel. Carbide axial face seals or specially designed radial shaft seals are used for sealing between the mixer and mixing chamber. The temperature of all mixing heads can be controlled and the heads can be equipped with shut-off systems to ensure stable mixing conditions. A sophisticated modular system made up of various mixing chamber sizes and geometries enables optimum adaptation of the mixing system to specific applications.
- MK107 model series
The MK 107 model series covers a dispensing output range of approx. 1 - 10 g/s. The mixing heads in this series can be equipped with up to three component valves, one flushing valve, and one blowing valve. - MK 108/111 model series
The MK 108/111 model series covers a dispensing output range of approx. 0,01 - 1,5 g/s. The mixing heads in this series can be equipped with two component valves, one flushing valve, and one blowing valve Modellreihe MK 200
Die Modellreihe MK 200 ist konzipiert für die Vermischung von pastösen Klebstoffen bis ca. 5 - 200 g/sec. Ein weiteres Einsatzgebiet ist die schonende Mischung von scherempfindlichen Materialien.
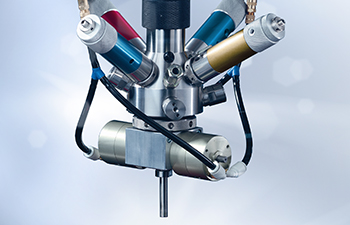
The MS-C is a compact, dynamic mixing system for precise metering, mixing, and dispensing. With a revolutionary, servo-driven ceramic valve system the MS-C sets new standards in productivity and reliability. The lean and compact design guarantees a higher degree of flexibility and allows dispensing of complex parts and applications. The simple modular design and the consequent separation of valve level and mixing chamber level make the MS-C the most maintenance-friendly mixing system available on the market.
MS-C 76 model series
The MS-C 76 model series covers a dispensing output range of approx. 0,1 - 2 g/s. The mixer and mixing chamber simply need to be adjusted to the materials' reactivity.MS-C 100 model series
The MS-C 100 model series covers a dispensing output range of approx. 2 - 120 g/s. Various mixing chamber geometries are available for the many different materials.
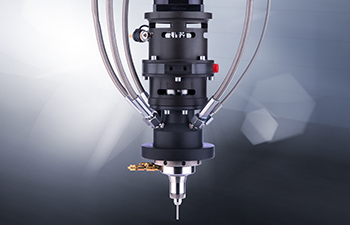
The static mixing head is used to mix materials that are highly viscous or have a paste-like consistency. Due to the high operating pressures, a steel tube is used to stabilize the disposable plastic mixer. A shut-off system that operates without any displacement ensures a clean thread break and a smooth transition. This system can be used in a dispensing output range of approx. 0,05 - 10 g/s.
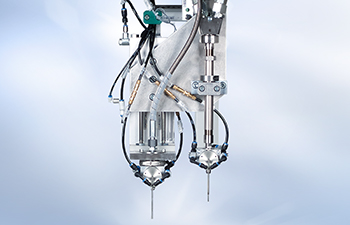
The MS-SC static mixing head is equipped with diaphragm valves and is therefore suitable for mixing highly abrasive materials. These valves also have a suck-back effect that ensures a clean thread break. There are no moving parts in reacting material.
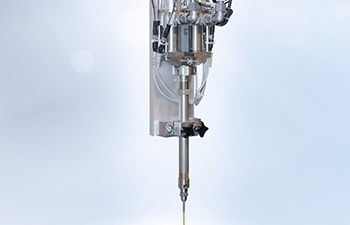
The most commonly used types of pumps in dispensing systems are external gear pumps. They are among the most precise dosing pumps and are suitable for dosing pressures of up to approx. 100 bar and low abrasive fillers. Wear-inhibiting coatings and optimized cog shapes increase service life.
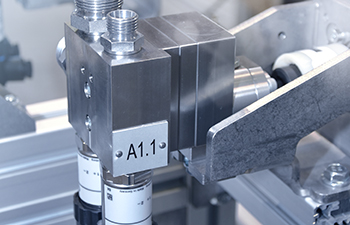
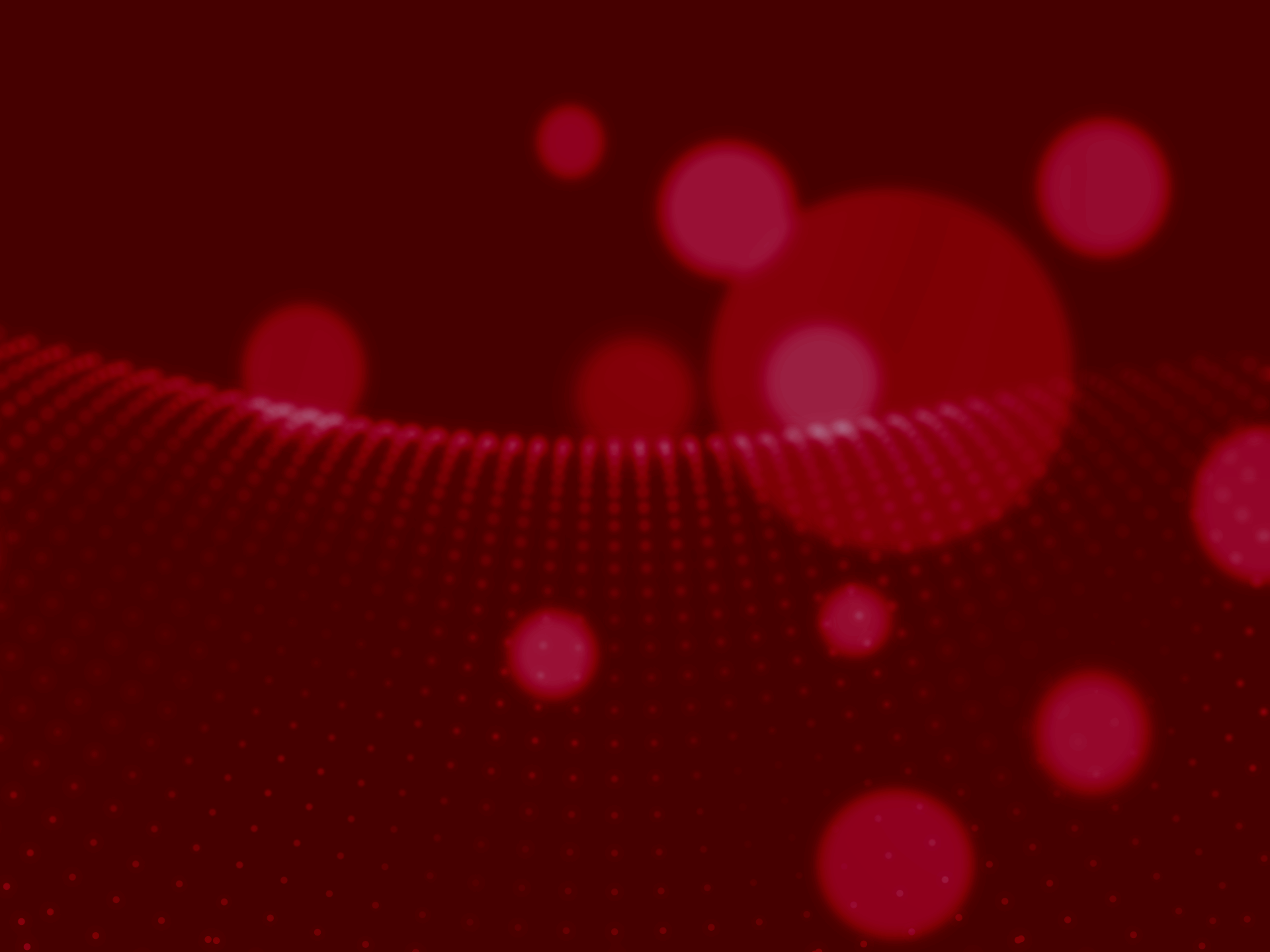
RAMPF Contact
Contact us – worldwide and around the clock!
- Please select