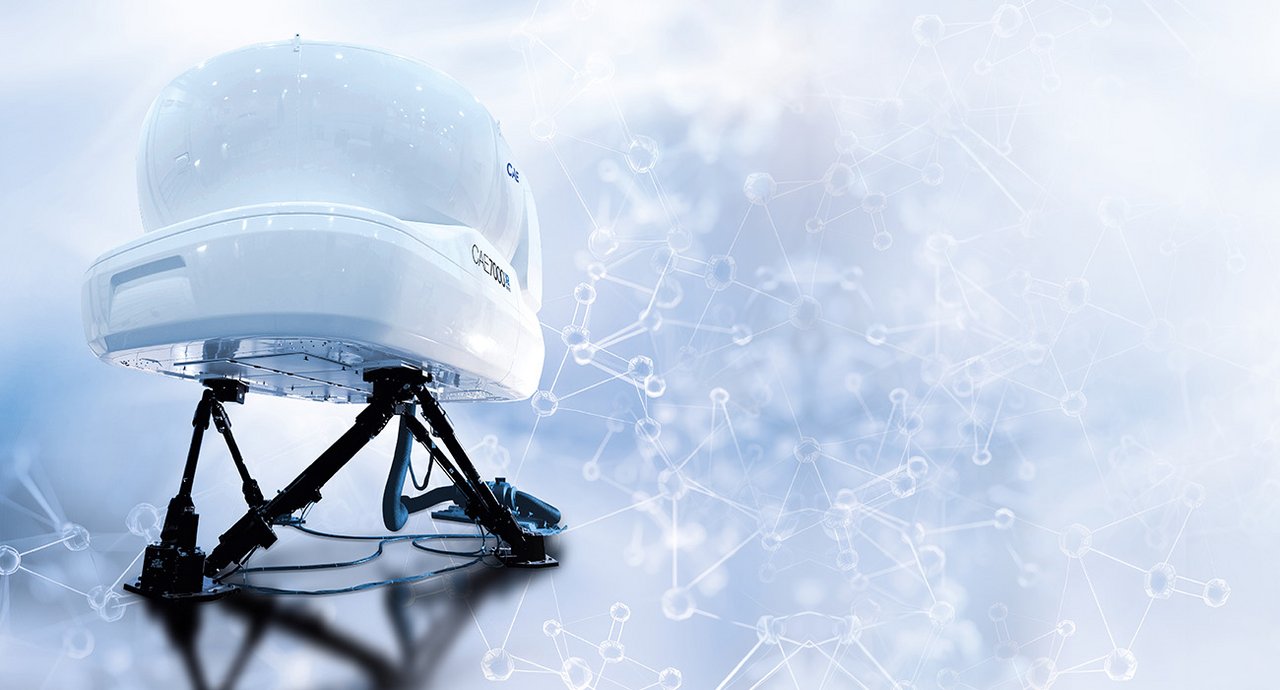
How RAMPF halves the time-to-market for customers
More than 200,000 aircraft transport passengers or freight between the world's airports every day. The pilots bear an enormous responsibility for the valuable cargo and must be specially trained. Pilot training requires hundreds of hours in a simulator before you ever go near a real commercial aircraft. Pilots must regularly practice in the simulator in a variety of complex situations and environments to ensure they are ready before they take the controls of a jet that costs hundreds of millions of dollars.
And this is where RAMPF comes into play, because RAMPF Composite Solutions, together with RAMPF Tooling Solutions, has reduced the time-to-market by 50 percent for components used by one of the leading manufacturers of flight simulators. The special feature: the entire process, from the concept to the turnkey components, was completely in the hands of the RAMPF experts, who used the RAKU® TOOL board material WB-0801 to produce the master pattern and then used the resin infusion process with RAMPF infusion resins to produce the mold and final composite parts for the railing kit for their best selling full motion flight simulator.
The advantages for the customer are obvious: a turnkey solution for model production, mold construction and production-ready parts. The board material WB-0801, which was used to produce the master model, has many advantages including the ability to mill it quickly and with high-precision directly from CAD data, a high-quality surface finish, and very good dimensional stability and dimensional accuracy.
Visitors to JEC World, which takes place in Paris from March 5 to 7, 2024, will also be able to experience these unbeatable benefits for themselves. At the RAMPF booth in Hall 5, Booth 5G117, visitors can expect threefold composite expertise: RAMPF Composite Solutions, RAMPF Tooling Solutions, and RAMPF Group, Inc. will be presenting their comprehensive product and service portfolio for the cost-effective production of high-performance composite parts.
RAMPF Composite Solutions: More Automation. Lower Costs.
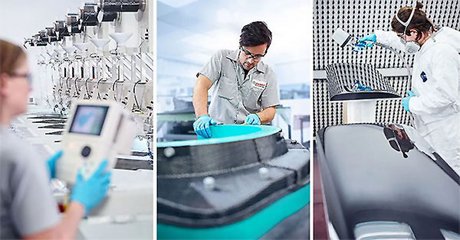
Quicker time-to-market at lower costs – RAMPF Composite Solutions is presenting holistic engineered solutions for technologically advanced composite design in the aerospace, defense, transportation, medical, and green technology industries.
The company’s experts make composites manufacturing more automated and less costly by using
- Cutting-edge Tailored Fiber Placement (TFP) technology
- Tooling materials with outstanding mechanical properties
- High-performance liquid resin systems
Together with material qualification, built-in quality assurance, and automation processes, subsystems and fully scalable prototypes are manufactured within days or weeks of design stage via an innovative one-shot solution.
Together with material qualification, built-in quality assurance, and automation processes, subsystems and fully scalable prototypes are manufactured within days or weeks of design stage via an innovative one-shot solution.
RAMPF Tooling Solutions: Three Top Epoxy Boards!

Unparalleled high-performance epoxy boards for the production of prepreg lay-up tools and vacuum forming molds – RAMPF Tooling Solutions presents the four high-tech board materials RAKU® TOOL WB-0691, WB-0700 and WB-0890 for applications in racing sports, marine, aerospace, and medical technology. The benefits:
- Wide temperature application range (HDT 110 - 140 ºC)
- Superior surfaces – reduced finishing effort, less sealer required, high edge strength
- Fast and easy to process – excellent milling properties and minimal dust
- Compatible with all paints, release agents, and epoxy prepregs in line with industry standards
- Adhesives that match temperature resistance and hardness of boards
The product portfolio of RAMPF Tooling Solutions for composite manufacturing also encompasses liquid systems based on epoxy (infusion resins, laminating resins, gelcoats) and Close Contour materials (Close Contour Paste, Close Contour Castings, Close Contour Blocks).
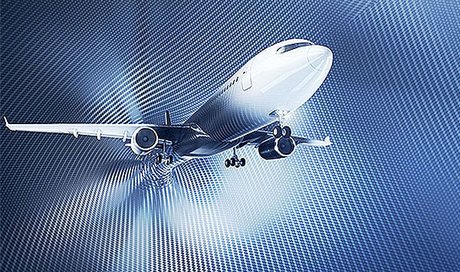
Minimal weight and maximum safety – RAMPF Group, Inc. is presenting its comprehensive range of epoxy liquid systems for composite production.
These are used, amongst others, in special mission aircraft for surveillance, firefighting and air refueling, as well as in helicopters and individual and regional air mobility.
Minimal weight and maximum safety – RAMPF Group, Inc. is presenting its comprehensive range of epoxy liquid systems for composite production. These are used, amongst others, in special mission aircraft for surveillance, firefighting and air refueling, as well as in helicopters and individual and regional air mobility.
The product highlights at JEC World 2024:
- RAKU® TOOL EI-2510 – the high-temperature, toughened epoxy system exhibits excellent hot-wet properties (dry Tg 210 °C, wet Tg 174 °C), high fracture toughness, and is used for a wide range of structural applications in high-temperature environments; the low-temperature processing 2-component resin requires less investment in tooling and infrastructure and no special storage.
- RAKU® TOOL EI-2511 – high-performance, flame-retardant structural resin with a high Tg (dry 165 °C, wet 137 °C); the epoxy system exhibits low viscosity at low processing temperature (200 mPas at 40 °C) and fulfills 12 and 60 sec vertical burn as well as the oil burner test for firewalls, engine nacelle components, and cargo liners.
- The combination of RAKU® TOOL EI-2510 and RAKU® TOOL EI-2511 with Close Contour Castings and high-performance tooling boards enables the cost-effective production of qualification-compliant components within days to weeks.
- RAKU® TOOL EI-2518 – flame retardant product for 12 and 60 second vertical burn requirements as well as application dependent UL94 requirements.
- RAKU® TOOL EI-2524 – epoxy resin infusion system with excellent processing characteristics and a wide range of hardener options. Suited for a wide range of applications ranging from Structural components in aerospace, Marine and various industries.
With its comprehensive range of products and services, the US subsidiary of the international RAMPF Group has established itself as a technology and quality leader in the NAFTA markets.
Visit the Lightweight RAMPF Trio at JEC World 2024 – Hall 5 / Booth 5G117!