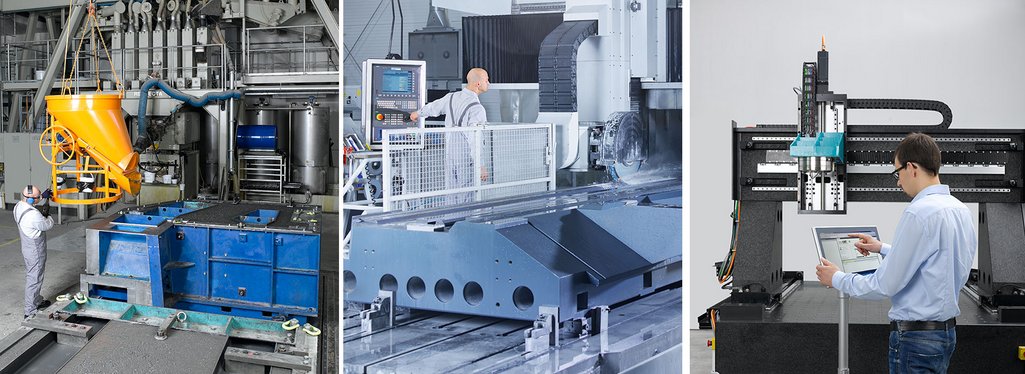
Domestic Sourcing – Supply Security in Times of Crisis
The best technology is only of use if it is available just in time, i.e. at the desired time, in the required quality, and in sufficient quantity. RAMPF Machine Systems ensures this with five production plants on three continents, a worldwide sales partner network, and an all-encompassing solution offering that is unique in the market.
A significant drop in or even a cancellation of orders, short-time work – the corona pandemic is hitting the already struggling mechanical engineering industry very hard. While the vast majority of companies suffered significant sales losses, the number of companies whose international supply chains are stalling is also increasing.
Temporary plant closures have led to the collapse of entire value chains. Even projects that could have been successfully carried out despite the crisis are being delayed. Significant delays are also likely when operations are ramped up again. Nevertheless, there is an opportunity in every crisis.
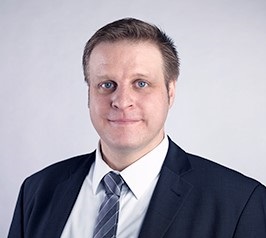
Dr. Thomas Abel, Director of Laboratory at RAMPF Machine Systems:
In contrast to gray cast iron, which is mainly produced outside of Europe, domestic sourcing has been the focus of RAMPF Machine Systems’ operations for over 40 years. This not only makes our products more climate-friendly, but also crisis-proof. Our alternative machine bed materials – mineral casting and ultra-high-performance concrete – also offer significant technical and economical advantages over gray cast iron.
Complete solution provider with global presence
For machine beds and machine bed components based on alternative materials, RAMPF Machine Systems stands for security of supply even in times of crisis. Why? Because the company has:
- a total of five production sites on three continents – three in Germany and one each in China and the USA.
- a worldwide sales partner network that ensures prompt support on site.
- a CAD design office equipped with the latest IT, in which innovative and future-oriented machine beds and machine bed components as well as molds, casting gauges, and fixtures are constructed via PTC Creo; if required, FEM calculations are also carried out.
- its own development and testing laboratory, maintains close cooperation with educational facilities, and is therefore always at the cutting edge.
- a powerful PPS system for optimal production planning and secure delivery dates.
- a specially developed mineral casting replication technology, with which straightness and flatness of 0.02 millimeters can be achieved with an impression length of 4 meters.
- its own grinding center in which machine frames made of mineral casting, ultra-high-performance concrete (UHPC), and hard stone are processed with the highest precision.
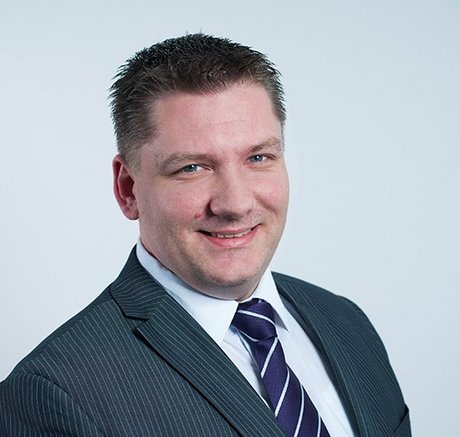
Marc Dizdarevic, CEO Technology & Sales of RAMPF Machine Systems:
We offer our customers a complete range of solutions that is unique in the market – from material-specific design and engineering, production, and assembly to system solutions, customized multi-axis moving systems, and basic machinery. As part of the international RAMPF Group, a globally active and diversified group of companies with more than 900 employees and an annual turnover of 190 million euros*, we stand for long-term security and reliability. And last but not least – with their quality-conscious and efficient way of working, our highly qualified and motivated employees ensure that our products are delivered on time and in the desired quality and quantity – also in times of crisis.
*Fiscal Year 2018/19