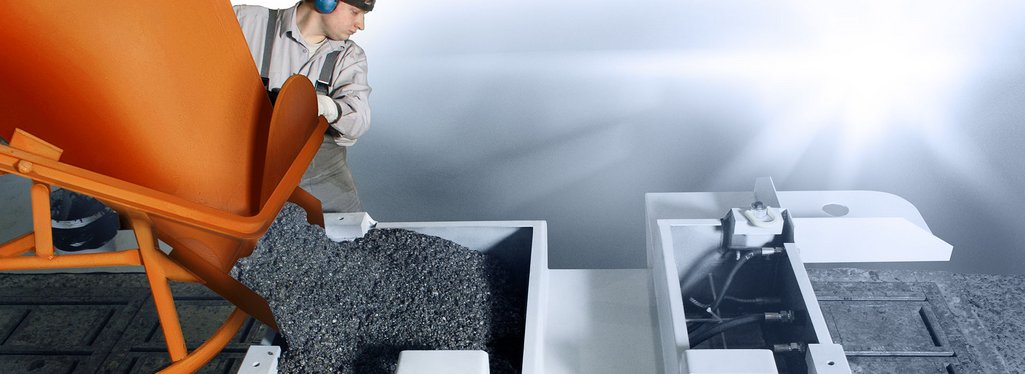
An Ultra-Stable Combination
- EPUFILLThe steel shell is filled in the following steps: Dosing, mixing, filling, compacting, curing. The raw materials must be precisely dosed and mixed. Depending on the viscosity of the filling material and depending on the filling geometry (e.g. wall thickness), compaction is brought about during the filling process by vibration and/or vibration.
- EPUFILL Teil 2Precision machining: Milling, drilling, grinding and scraping are available for precision machining. Manufacturers recommend applying the final accuracy to the filled frame component only after it has fully cured (approx. one to two weeks after filling).
- EPUFILL Teil 3Dynamic properties: The special feature of hybrid frame assemblies is that the material composite produces new properties, which are generally desirable. For example, damping filler materials have a positive influence on dynamic properties such as vibration amplitudes and natural vibration modes, which also reduces noise emissions. The greater mass of steel composite structures generally has positive dynamic effects.
- EPUFILL Teil 4Thermal behavior: Due to the high specific heat capacity and low thermal conductivity of EPUMENT mineral casting, the steel composite construction reacts less sensitively to short-term temperature fluctuations. In addition, cooling or heating pipes can be cast in to control the temperature of frame components.
- EPUFILL Teil 5Static behavior: The overall static behavior of composite steel structures is also influenced by both the steel shell and the infill. The modulus of elasticity, the strength of the filler materials and the wall thicknesses of the sheathing steel are important in this context.
The filling of steel and cast structures with epoxy resin-bonded mineral casting is a well-established technique. More than that, machine bed assemblies are increasingly being designed as hybrid structures from the outset – using EPUFILL technology from RAMPF Machine Systems.
Cavities in steel or gray cast iron machine bed components have been filled with castable materials, usually epoxy resin-bonded mineral casting or cement-bound concrete, since the start of the 1980s. This technique has thus been tried and tested for more than three decades, and has been finely tuned throughout this period.
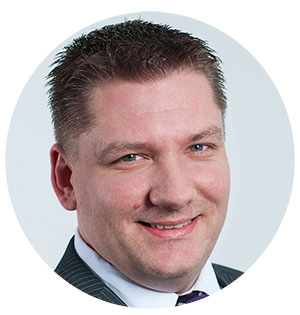
Marc Dizdarevic, CEO of RAMPF Machine Systems, confirms this:
At first, cavities were often filled in a subsequent process to improve dynamic performance. Since then, this technique has become a process in its own right that is offered on an industrial scale, i.e. machine bed assemblies are designed with a hybrid structure from the outset.
EPUFILL – outstanding damping properties guaranteed
RAMPF Machine Systems adopted this technology early on and has established a dedicated division – EPUFILL. This is where structures that are welded or cast, made of steel or comprised of a metal shell are filled with the in-house product EPUMENT® mineral casting. The key benefits include much better damping properties and more favorable thermal component behavior due to the greater thermal capacity.
“We made a conscious decision to opt for filling with epoxy resin-bonded mineral casting. The crucial advantage of this compared to filling with water-based concrete is that the filling material adopts a solid bond with the outer sheath, thereby creating a composite structure with excellent long-term stability,” explains Dizdarevic.
The text below focuses on steel composite structures filled with EPUMENT® mineral casting.
Key parameters for the long-term stability of machine bed components with consistent properties throughout their service life include the adhesive force between the hybrid partners and the moisture absorption of the filling. This is where mineral casting differs greatly from concrete as a filler material. Given identical sand-blasted contact surfaces, concrete achieves a maximum of 50 percent of the bonding strength with steel. Due to the very high moisture absorption of concrete fillings, the pouring surface also needs to be sealed.
Marc Dizdarevic sums up the technology’s benefits:
Using EPUFILL technology to manufacture machine bed components is worthwhile first and foremost when dealing with small order quantities, such as when producing prototypes and special machines that need to accommodate high static and dynamic stresses. This technique saves the high one-off costs of the mold while still utilizing the numerous advantages of mineral casting.