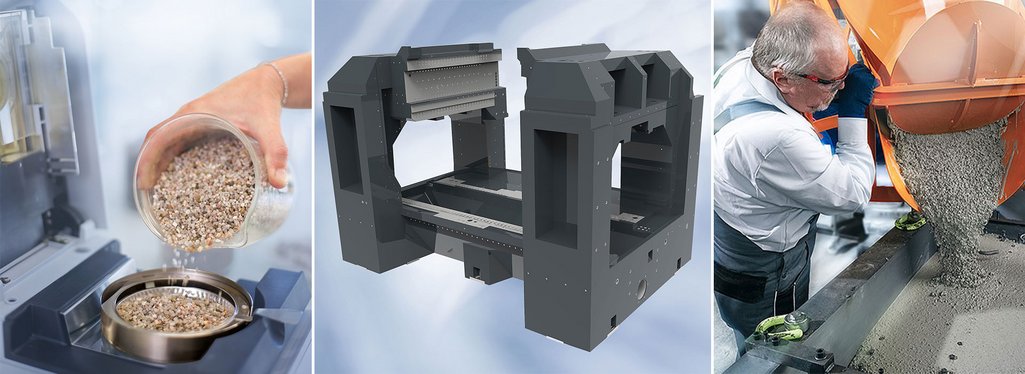
How to (1) – Manufacturing Mineral Casting Components
From producing the casting mold to mixing the mineral casting ingredients to painting the finished part – here is the exciting story of how a high-tech machine component made of EPUMENT® mineral casting from RAMPF Machine Systems is manufactured.
- Compared to gray cast iron and welded constructions, it features significantly better damping properties. This ensures that the machine bed structure has greater dynamic stability in ultrafast and high-precision production machines.
- Its outstanding thermal stability means that it is less readily affected by short-term temperature-related influences.
- Its ecological credentials are outstanding thanks to the resource-saving production as well as environmentally friendly disposal and recycling.
These are just three of numerous major advantages of EPUMENT® mineral casting.
It is therefore not surprising that the innovative material has long since established itself in high-tech mechanical engineering and is being used in many industries around the globe – from classical machine tool construction to the semiconductor, laser, medical, and packaging industries.
But how are high-performance machine components created by mixing minerals, stones, and epoxy resin binders?
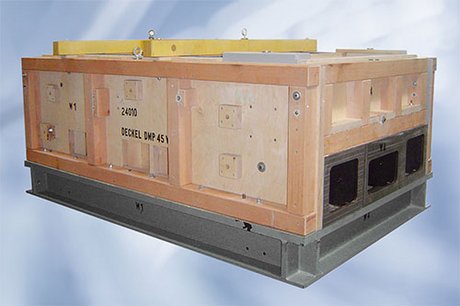
1. Manufacture of casting mold
In general, casting molds are manufactured by specialized tool and mold makers and also approved by them. The advantage is that any errors and deviations can be immediately rectified. After this, the casting mold is delivered to RAMPF Machine Systems, dismantled into its individual parts, and placed on assembly stands / devices or fixed in an upright position.
2. Cleaning and coating with release agent
The inside of the mold must be thoroughly cleaned. To prevent the mineral casting from sticking to the inside of the casting mold, the entire inner surface of the mold is coated with a special release agent, usually via spraying. Cast inserts such as thread anchors, base plates, and pipes are fixed by screwing / plugging onto the inside of the casting mold.
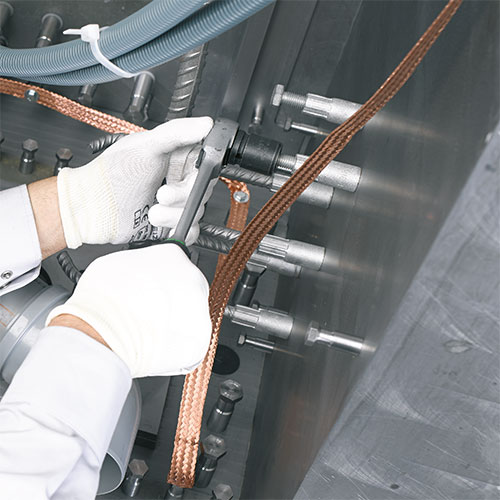
3. Gelcoat application
The gelcoat is applied via brushing or airless spraying in a layer thickness of 0.5 mm to 2 mm on the inside of the molded parts. The surfaces that will be molded or bonded at a later stage are left out. The gelcoat bonds with the mineral casting to form a resistant surface layer. Properties such as scratch and temperature resistance can be adapted to customer requirements. The gelcoat can be produced in most RAL colors and serves as a primer for painting. Finally, the molded parts are screwed together and pinned to the molding base.
4. Dispensing, mixing, casting, compressing
The components of the mineral casting are dispensed, mixed, and cast into the mold. After compression, hardening takes place in the casting mold.
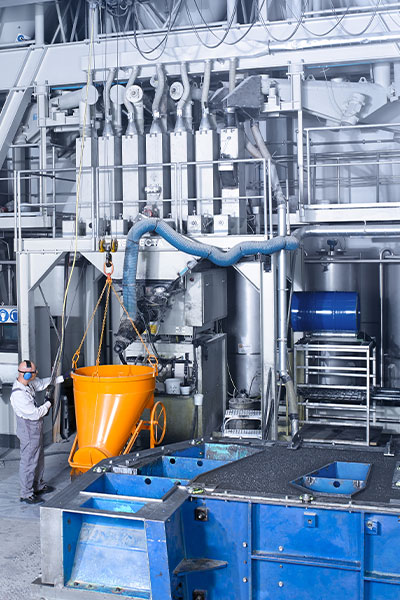
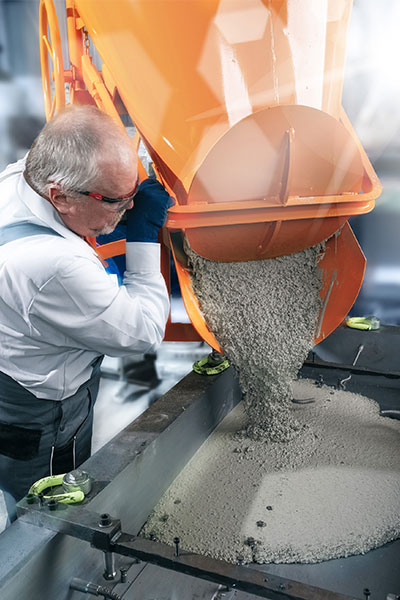
5. Compressing
The compression process ensures the best possible ventilation of the mineral casting mixture and improves the flow properties of the viscous mass. The relative movement of the filler components during vibration reduces the pore content. Especially when compressing large-volume parts in heavy casting molds, better results are achieved with so-called compression tables. The influence of parameters such as acceleration, amplitude, frequency, and duration on the compression process and thus the final properties of the mineral casting have been studied. In industrial settings, these parameters are set individually for each casting depending on the fill weight, fill level, and casting mold material. Modern compression tables are continuously adjustable up to a frequency of 70 Hz and an accelera-tion of 25m/s2 (2.5g).
6. Curing
For curing, the filled casting mold is mounted horizontally in the assembly hall, as the restricted position of the casting mold would result in a cast blank that is not dimensionally accurate during curing. Because steel molds dissipate heat more quickly from external mineral cast layers than from the core, thermal insulation of the casting mold is recommended for large components. The objective is an uniform temperature development over the entire cross-section of the cast part; this can be controlled by embedded temperature sensors. The curing speed is influenced by the outside temperature and the reactivity of the hardener. After 12 to 14 hours of hardening in the casting mold, the casting blank can be removed. As a rule, one mineral casting can be produced per casting mold per working day.
7. Demolding
When dismantling the casting mold, the fastening screws of the inserts are removed and the molded parts pressed off the cast blank in reverse order of assembly. The cast blank is then lifted from the bottom of the mold and all loose parts are removed from the blank.
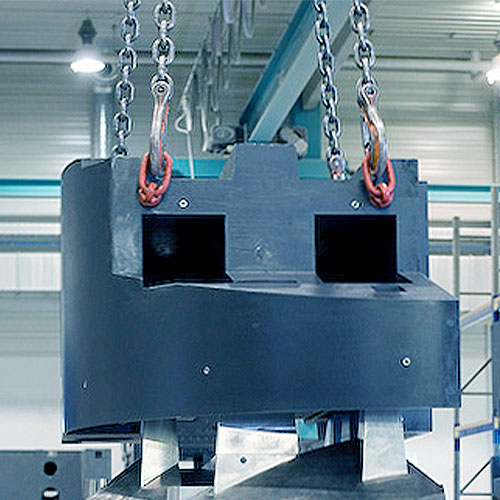
8. Cleaning
Thanks to cold casting in precise forms and high-performance gelcoat systems, the cleaning of mineral casting blanks made is generally less time-consuming compared to those made of gray cast iron. The surfaces already have a good optical quality and often meet the necessary requirements after the release agent has been washed off. Components that take on design and cladding functions on machines must be cleaned on the corresponding surfaces. At the joining surfaces of the casting mold segments, burrs occur on the cast blank, which are sanded off with hand grinders. Other surface defects such as chippings, impressions, and surface cavities are also eliminated during cleaning. The gelcoat surface is sanded before painting. Furthermore, the cleaning process prepares the surfaces that are to be molded or bonded. As already mentioned, these surfaces are not coated with gelcoat. The mineral casting surface is roughened with hand grinders. After molding or bonding, protrusions are sanded off.
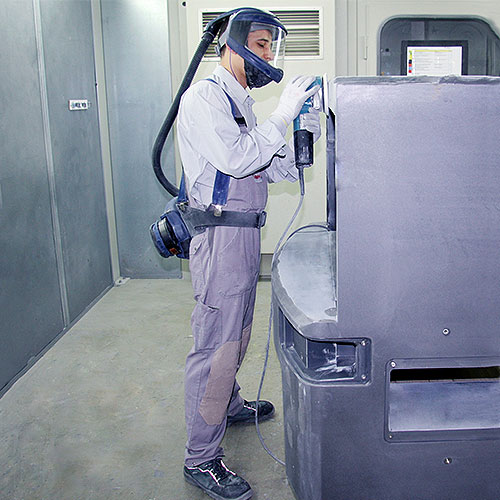
9. Refining of casting surface
The casting area is open, non-form specific, and therefore slightly uneven. As a rule, however, this is not problematic, as it is usually the underside of the frame. In the case of higher requirements, the surface can be optically refined by applying a cast coating.
10. Painting
Mineral casting parts can be painted in practically any color, with the paint being applied by spraying or rollers. Since many casting parts are already integrated in the blank, care must be taken to protect internal threads. Separating and cleaning agents, gelcoats, and paint must be precisely chemically aligned to one another.
The result of this process tells its own tale, amongst others with the machine bed (left) of the STAMA milling-turning center MT 733 two plus (right):
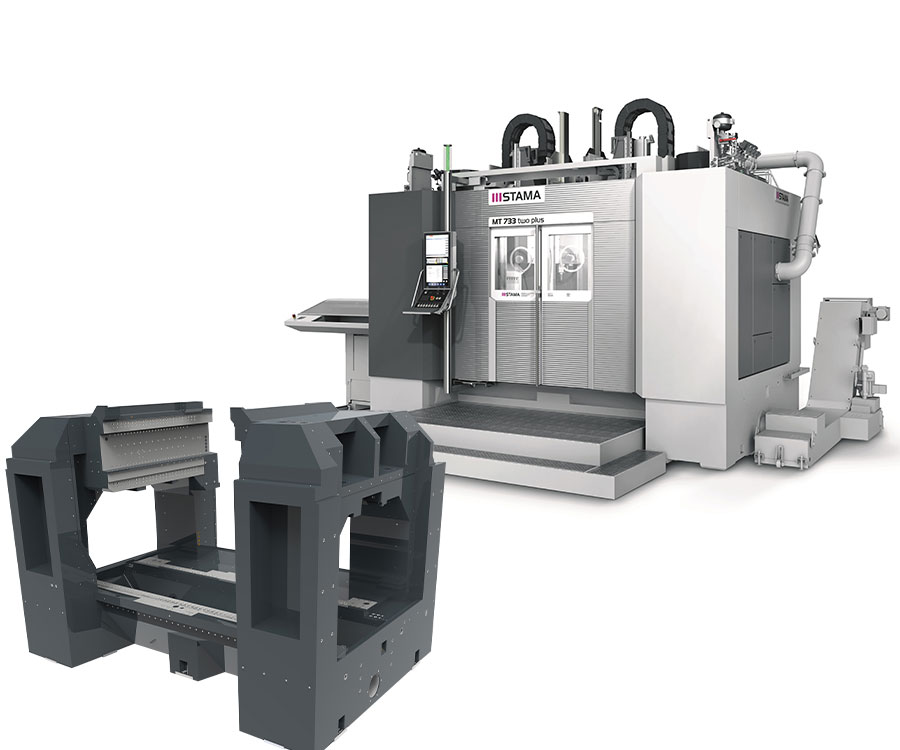