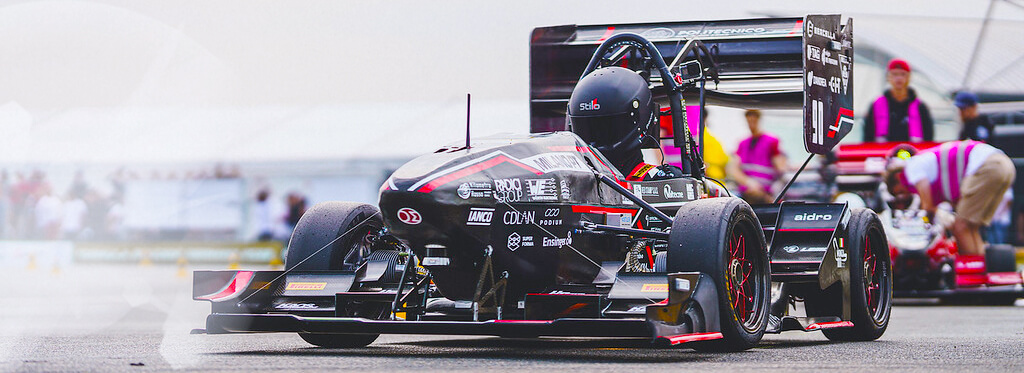
Nothing less than victory!
With RAKU® TOOL CC-6503
Production of a formula student monocoque using Close Contour Casting RAKU® TOOL CC-6503 for the master models.
Working together with creative and committed young people is always something special. This is certainly true for the members of Dynamis PRC, the formula student team from Politecnico di Milano, Italy.
The team’s racing cars featuring carbon fiber monocoques are very successful – but the students are not resting on these laurels. In 2022, they did something completely new and developed a car that competed in both the electric vehicle and driverless vehicle categories.
For this, the monocoque had to be fundamentally re-engineered to accommodate the new system. To meet this challenge, Dynamis PRC chose RAMPF’s Close Contour Casting RAKU® TOOL CC-6503 to produce the master models of the chassis. The master models were then used to manufacture lay-up tools with low-temperature prepregs.
Production of master models with Close Contour Casting RAKU® TOOL CC-6503.
Dynamis PRC chose Close Contour Casting for:
1. Quality
- Fine and homogeneous surface quality due to high density. Perfect surface roughness.
- Very high dimensional stability thanks to minimum residual stresses during special RAMPF casting process.
The alternative solution of bonded boards can generate tiny slots that result in local resin deficiency or accumulation, so was therefore not chosen.
2. Efficiency
- Extremely efficient technology when compared to board bonding. Reduction of material waste, machining times, tool wear and costs. The machining allowance is just approx. 10 mm thick. This difference is particularly accentuated by the monocoque geometry with the split junction line.
- Optimization of human resources and reduction of production times: no bonding, less finishing due to high surface quality.
3. Sustainability
- Reduction of waste during milling.
- Fewer chemical products are needed to achieve an excellent surface quality.
4. Savings in Production Time & Cost
Total production time was drastically reduced, with a total of 4 days for milling and less than 3 days for the pre-processing of the models:
| Operators | Days |
Milling | 1 | 4 |
Sanding | 3 | 1 |
Polishing | 2 | 0.5 |
Pore Filler | 2 | 0.5 |
Release Agent | 2 | 0.5 |