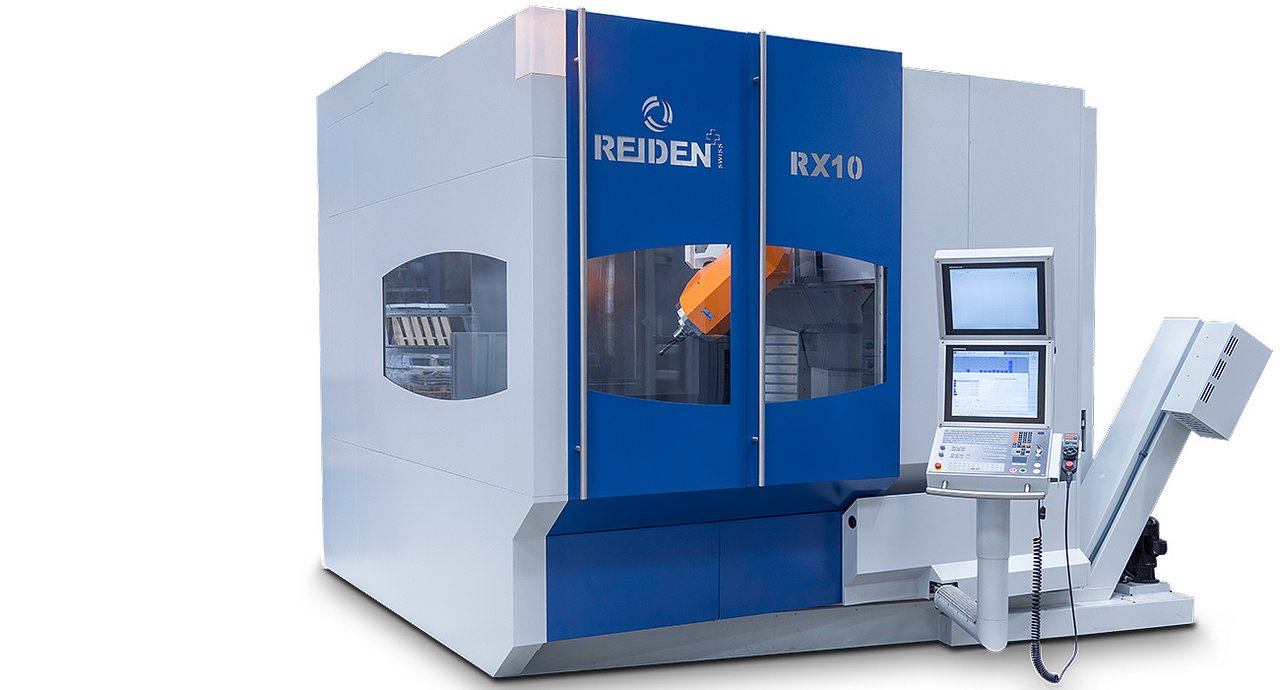
Energy-Efficient. Space-Saving. Ultra-Stable. REIDEN RX10 with EPUMENT Mineral Casting.
Minimierung der bewegenden Teile, Maximierung der ruhenden Masse: Das Konstruktionsprinzip des markführenden 5-Achs-Bearbeitungszentrums RX10 der Reiden Technik AG ist Programm. Auch dank eines schwingungsdämpfenden und energieeffizienten Maschinenbetts aus EPUMENT® Mineralguss von RAMPF Machine Systems.
5-axis machining center RX10 from Reiden Technik AG
- 1. Very small footprint with large machining area
- 2. DDT Double Drive Technology drive concept with speed of 18,000 rpm and maximum torque of 291 Nm
- 3. Active temperature control of machine bed and stand for 24/7 operation
EPUMENT® mineral casting from RAMPF Machine Systems
- 1. Outstanding vibration damping for ultra-fast and high-precision machines
- 2. High degree of functional integration – cold casting process enables direct integration of sensors, actuators etc. in machine bed
- 3. Resource-saving production, environmentally friendly disposal, recyclability
“Space-saving marvel” – this is how customers describe the RX10 in view of its compact appearance and yet very large machining area. The 5-axis machine for milling and turning is designed for optimal space utilization, with the ergonomic arrangement of the control elements ensuring best operability, even in the tightest of spaces.
Daniel Lustenberger, Head of Marketing & Sales at the Swiss machine tool manufacturer Reiden Technik AG:
Just as impressive is our DDT Double Drive Technology spindle concept. While the standard version is equipped with a motor spindle variant generating a speed of 16,000 rpm and a maximum torque of 135 Nm, our patented DDT drive concept achieves up to 18,000 rpm and 291 Nm.
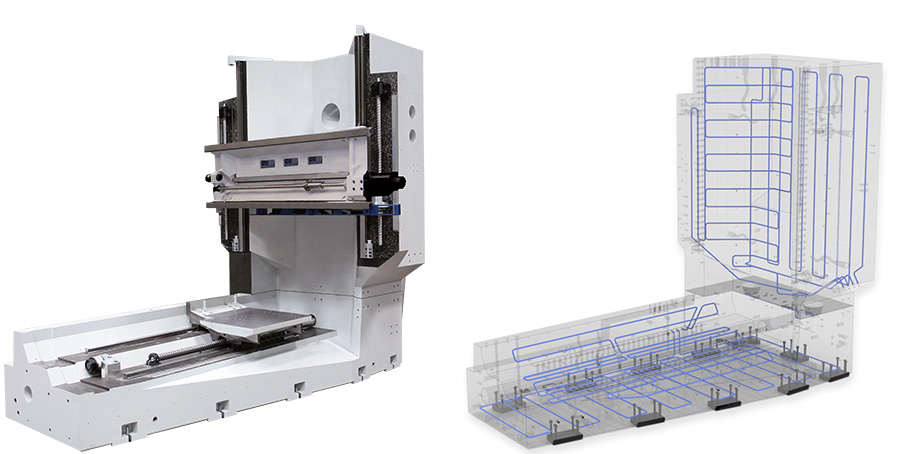
A further benefit of REIDEN RX10 is the active temperature control of the machine bed and stand. Thanks to the energy-optimized cooling unit, the closed system can be operated continuously, even overnight or during downtimes. In addition, the machine can be run at ambient temperatures and therefore offers a very high level of geometric accuracy, also under difficult conditions.
This is made possible by 200 meters of cast-in temperature control lines in the machine bed made of EPUMENT® mineral casting from RAMPF Machine Systems.
The integrated line system ensures effective dissipation of process heat and thus thermally stable production processes, which guarantee maximum precision and quality,
Daniel Lustenberger points out.
Kacper Lasetzki, Sales Manager at RAMPF Machine Systems, adds:
EPUMENT® is cold cast into molds and cures at room temperature, which means that almost all functional elements can be installed before casting. This reduces both the amount of post-processing work and the delivery time.
Maximum vibration damping. Sustainably produced and recyclable.
EPUMENT® mineral casting ensures maximum dynamic stability of the frame structure for ultra-fast and high-precision machines. Comparative measurements of the logarithmic decrement as a damping parameter show that mineral casting has eight to ten times higher material damping than gray cast iron and welded constructions.
In addition to the unrivalled damping properties, the low CO2 footprint of EPUMENT® mineral casting is also a decisive competitive advantage. Thanks to cold casting and the extremely high casting accuracy, up to 75 percent primary energy is saved compared to gray cast iron, and CO2 emissions are 4.5 times lower. In addition, RAMPF mineral casting can be recycled as normal construction waste for fillers or soil stabilization.
Kacper Lasetzki:
We have been working successfully with Reiden Technik AG for over 17 years. The company has an outstanding reputation as a manufacturer of intelligent, customer-specific solutions in mechanical engineering. We are proud to contribute to this success both as a development partner and with our innovative machine bed material.