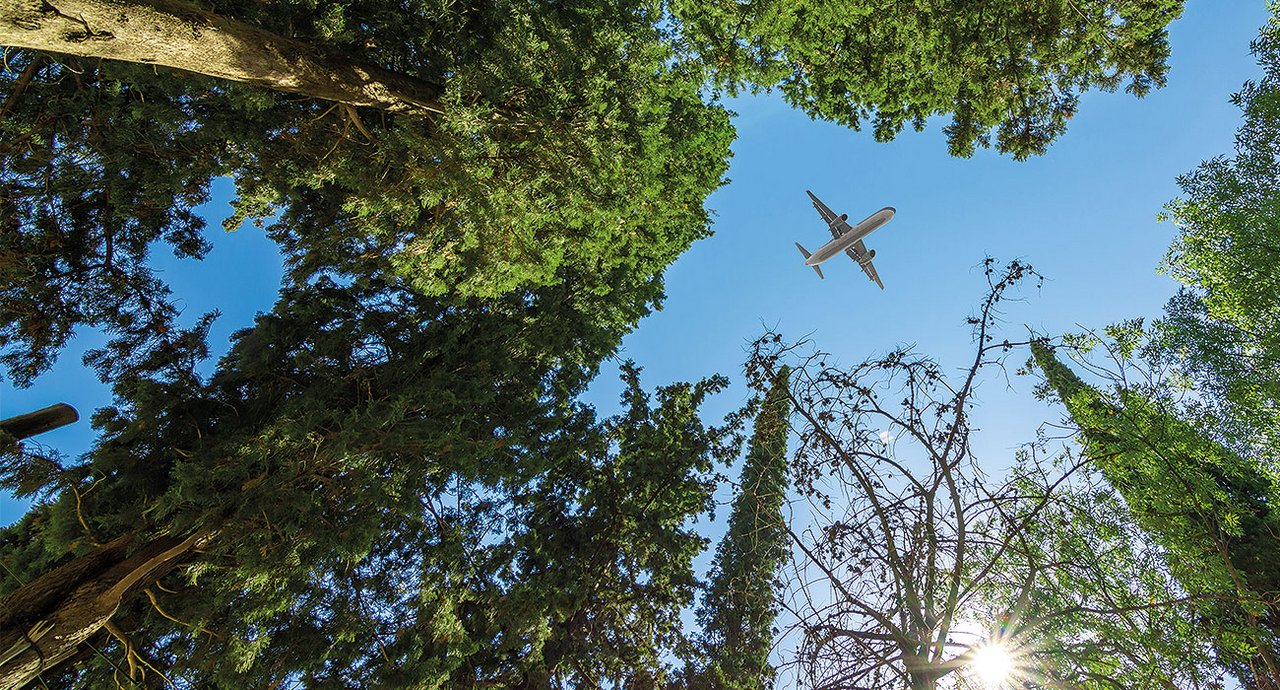
Strong Impetus for RAMPF's Journey Towards Net Zero Emissions
RAMPF Composite Solutions is utilizing the data from a comprehensive carbon footprint analysis to define targeted reduction strategies for achieving net zero emissions and further enhancing the company’s market competitiveness.
The use of composites technology in industries like aerospace, automotive, and transportation is enhancing sustainability by reducing vehicle mass and thereby lowering the energy required for the transportation of people and goods. However, as the composites industry grows, its environmental impact is also increasing.
Manufacturers, especially in aerospace, need to adopt sustainable practices.
RAMPF Composite Solutions is a leader in this effort. An in-depth carbon footprint analysis carried out by ClimaTech Innovations Inc. is now enabling the company to identify actionable strategies to achieve net zero emissions. The analysis suggests several measures to reduce emissions by up to 30.5 percent:
- Switching heating systems from natural gas to electricity
- Upgrading company vehicles and optimizing machinery for better energy efficiency
- Improving material use and logistics in the supply chain
Additionally, RAMPF is considering nature-based compensatory measures like planting trees and preserving forests to balance unavoidable emissions.
Larry Fitzgerald, CEO of RAMPF Composite Solutions:
RAMPF's rigorous approach to finding ways to reduce its carbon footprint sets a benchmark in the industry. This both supports global sustainability goals and enhances our market competitiveness, demonstrating leadership and innovation in composite solutions in industries such as aerospace, defense, industrial, medical, high-end consumer, and green transportation.
Reducing environmental impact and costs with Resin Infusion technology
RAMPF's innovative cutting-edge Resin Infusion technology is a prime example of the company’s approach to reducing its environmental impact.
This method provides a sustainable alternative to traditional prepreg techniques by eliminating the need for refrigeration and autoclaves, which are known for their high energy consumption.
Instead, parts are cured in lower-temperature ovens, significantly decreasing emissions compared to prepreg use.
Utilizing the benefits of Resin Infusion technology also results in a 30 percent cost saving over traditional methods.
Aerospace manufacturers using this eco-friendly technology can expect faster production times and lower costs while maintaining high-quality and reliable component manufacturing.
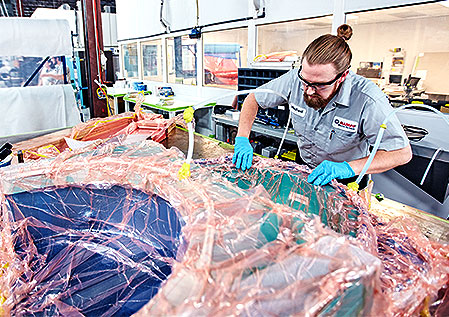