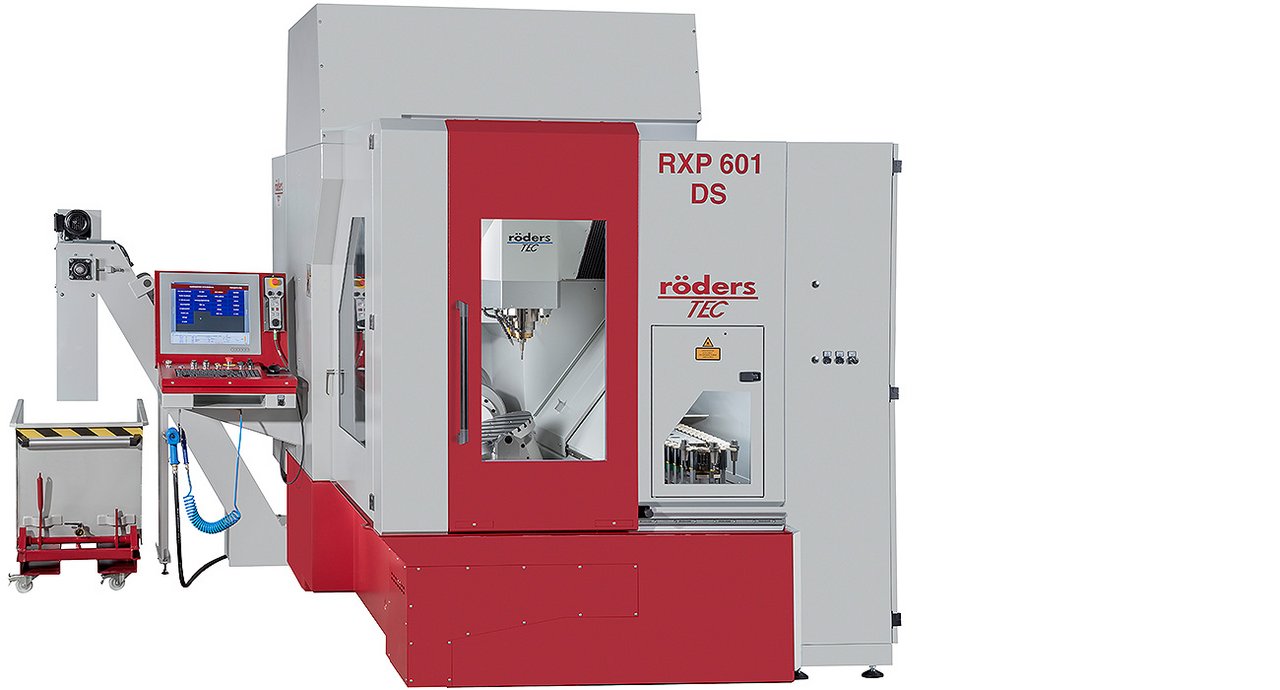
Machine Bed. Joining & Replication. Assembly. Painting. Röders TEC Relies On Comprehensive Service From RAMPF.
Röders TEC relies on the comprehensive expertise of RAMPF Machine Systems for material selection, joining and replication processes, cooling line installation, and painting to manufacture the machine bed for its high-performance 5-axis milling machine, the RXP601DSH.
Key Facts: 5-Axis Milling Machine RXP601DSH by Röders TEC
- Exceptional precision and machining performance for processing demanding materials, powered by frictionless linear direct drives and 32 kHz controllers across all axes.
- High correction frequency reduces machining times and ensures excellent surface quality.
- Innovative temperature management maintains the medium temperature within ±0.1 K, while the frictionless vacuum weight compensation in the Z-axis ensures high-precision coordinate grinding.
Key Facts: Complete solution for high-dynamic production technology by RAMPF Machine Systems
- EPUMENT® mineral casting delivers exceptional precision and dimensional accuracy, stability and rigidity, unparalleled damping properties, and outstanding carbon footprint.
- Mineral casting is cold cast, allowing functional elements to be integrated before casting, which reduces post-processing and delivery time
- RAMPF replication technology produces precision surfaces on machine bases without the need for costly machining processes.
Röders TEC, based in Soltau, Lower Saxony, Germany, is a pioneer in high-speed cutting technology (HSC). A prime example of this technological leadership is the HSC 5-axis milling machine RXP601DSH.
Jürgen Röders, CEO of Röders GmbH:
The RXP601DSH is engineered for the highest precision requirements and exceptional cutting performance, even with challenging materials like stainless steel and titanium. The frictionless linear direct drives and 32 kHz controllers in all axes ensure dynamic and highly precise machining. This high correction frequency significantly reduces machining times and ensures optimal surface quality.
The RXP601DSH is also ideal for coordinate grinding, featuring a patented, frictionless vacuum weight compensation in the Z-axis. Its advanced temperature management system ensures maximum thermal stability by precisely regulating the temperature of the circulating medium to within ±0.1 K.
The experts at RAMPF Machine Systems significantly contribute to the leading market position of the RXP601DSH with a machine bed made of vibration-damping EPUMENT® mineral casting. The bed is cast in two parts – upper and lower – and joined using the company’s proprietary joining technology.
Thanks to RAMPF's innovative replication technology, precision surfaces on the upper and lower parts are produced without the need for costly machining processes. The contours of highly accurate gauges are transferred onto the mineral casting blank using special coating systems (filled resins) in a climate-controlled hall at 20°C.
One-stop solution
Complex cooling channels are directly cast into the upper and lower parts to ensure precise temperature control of the milling machine, optimizing its thermal stability and accuracy. RAMPF also installs the guide rails for the X and Y axes.
Since the RXP601DSH is partially uncovered and some surfaces remain visible, RAMPF paints the machine bed in red and white.
Kacper Lasetzki, Sales Manager at RAMPF Machine Systems:
Machine beds made from EPUMENT® mineral casting offer the highest precision and dimensional accuracy, stability and rigidity, unparalleled damping properties, and an unbeatable carbon footprint compared to gray cast iron. Our joining and replication technologies also optimize the cost efficiency of the manufacturing process for high-dynamic production machines. We are proud to have contributed to the success of Röders TEC with this powerful complete package for over twenty years.