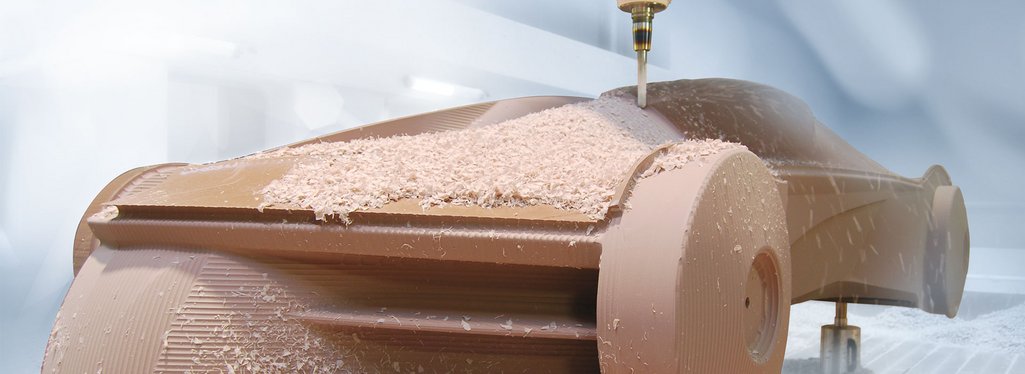
Close Contour Casting: Order it, mill it, and you’re done!
This blog post provides information about the machining and benefits and includes informative application videos.
- Quality
- Excellent mechanical properties
- Dense, homogeneous, seamless, and fine surface
- Easy to mill
- Cost-effective
- Savings, as less material used
- Reduced milling time thanks to close contour shape
- Sustainable
- Less waste, less material used
- User-friendly
- Not having to produce the casting (blank) means you can focus on the core technology / milling technology
- Casting is performed in-house by RAMPF Tooling Solutions in specially equipped and designed facilities. You receive a ready-to-mill casting (blank) that has a machining allowance and can be milled like board material.
How does Close Contour Casting work?
Close Contour Casting is a special casting process developed by RAMPF Tooling Solutions for manufacturing castings close to the final shape.
- VergussCAD data is used to produce a mold from lightweight molding material such as EPS or PU foams, taking shrinkage and machining allowances into account.
- EntformenThe mold is pre-treated with a release agent and then filled in a vacuum-assisted casting process.
- Entformen Teil 2The casting is demolded and tempered. Annealing gives the blank its final chemical properties and also reduces stress.
- FräsenAfter delivery, customers can concentrate exclusively on milling.
How do I order my Close Contour Casting blank and what should I take into account?
The specialists at RAMPF Tooling Solutions are happy to contribute their experience to help with the engineering or design of the Close Contour Casting, if required.
Designing the Close Contour Casting
When manufacturing Close Contour Casting using the shell-mold casting technique, the walls of the outer shell and the ribbing of the casting must be at least 60 mm thick. This also applies if the outer shell is 40 or 20 mm thick after machining. Due to casting reasons, this is an absolutely essential requirement.
The design and construction of the Close Contour Casting, the necessary machining allowances, and the Close Contour Casting’s ribbing and reinforcement are the customer’s responsibility.
Once the Close Contour Casting has been designed, a product-specific shrinkage allowance of 0.5 to 2% must also be factored in for manufacturing the casting.
The physical parameters for designing the casting can be found in the technical datasheets for the individual products. RAMPF Tooling Solutions guarantees the correctness of this data.
Important documentation for the manufacturing process at RAMPF
- We always require a drawing, sketch, CAD screenshot, or JPEG from the customer for every component to be manufactured, as this information is used as a point of reference for the mold dimensions.
- This information must be available when the order is received so that any uncertainties can be clarified before casting.
- Written dimensions, including the machining allowance, are sufficient for rectangular Close Contour Blocks (for details, see product data).
For Close Contour Blocks
The general rule is that RAMPF Tooling Solutions will only add a shrinkage allowance to the dimensions specified in the order. The customer has to assess how many mm of machining allowance is needed for the unmachined block. We generally recommend a machining allowance of at least 10 mm. Dimensions ordered = dimensions supplied, within the specifications. Close Contour Blocks are unmachined blocks that have undergone basic cleaning only – release agent residues may therefore be present on surfaces. Sharp edges are beveled due to the risk of injury.
For Close Contour Castings
For a dimension of up to 1,000 mm, an allowance of 20 mm must be factored in for each surface to be machined. All dimensions larger than this must contain a shrinkage allowance of 0.5 - 2% (depending on the product) + machining allowance of at least 10 mm for each surface.
It is advisable to discuss the individual project with the relevant staff from RAMPF Tooling Solutions.