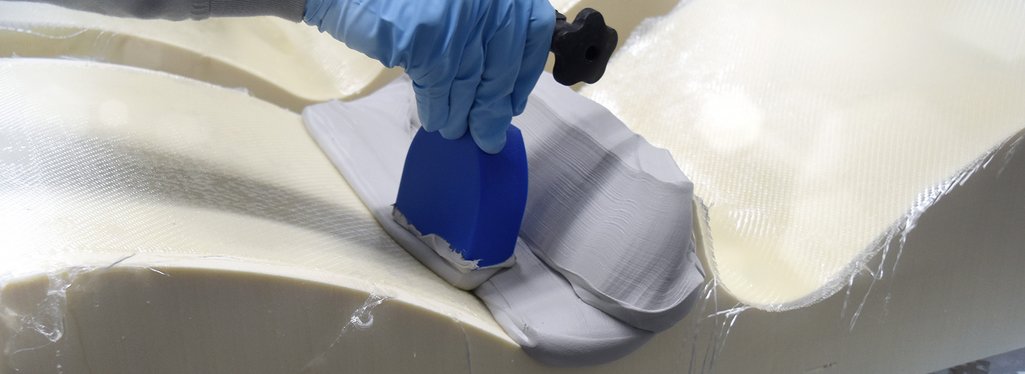
Shapely. Practical. Close Contour Paste.
Yes – it’s that easy to produce models, molds, and tools with RAKU® TOOL Close Contour Pastes. In the following blog, we would like to inform you about how Close Contour Pastes are processed and the numerous advantages they offer.
Why Close Contour Pastes? The main advantages:
Processing
- Thixotropic systems enable quick and easy processing with no slump on vertical surfaces.
- Application manually or via CNC machine.
- Components are processed via mixing & dispensing machines and can then be immediately applied.
Customer Benefits
- The close contour shape of the part significantly reduces milling time and production waste.
- Simple and low-cost substructure – virtually every material can be used, amongst others styling board RAKU® TOOL SB-0080, EPS, and cast aluminum.
- Less finishing required due to homogeneous, seamless surface.
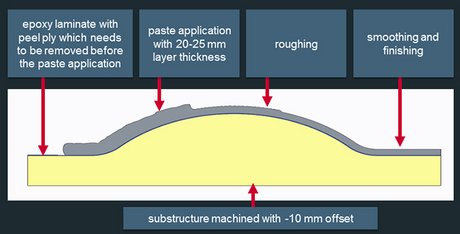
How is Close Contour Paste processed?
First, the substructure is selected according to operational conditions. It can consist of RAKU® TOOL SB-0080, EPS foam (minimum 20 kg / m3) with epoxy laminate, or cast aluminum. The substructure must contain -10% offset.
The paste is applied to the substructure in a layer thickness of approx. 20 - 25 mm and with an overlap. The nozzle must always be kept perpendicular to the surface. The exact application technique and section size depend on the chosen paste system, layer thickness, part contour, and temperature.
When the paste has cured according to the specifications listed in the technical data sheet, milling can start – first roughing, then smoothing and finishing.
The following clip contains detailed footage of the project with Phiaro Group, including the milling of the substructure, the application of the Close Contour Paste RAKU® TOOL CP-6070, and the milling of the final car model.