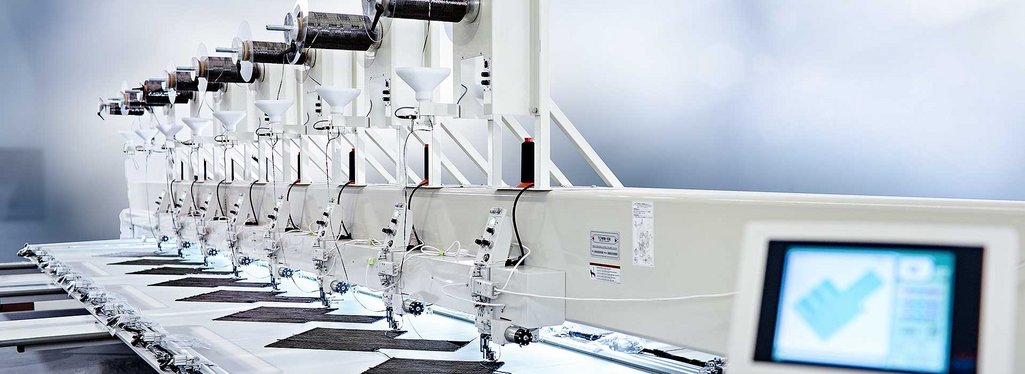
Mission Possible – lightweight & cost competitive
Reducing component weight and production cost – thanks to the experts from RAMPF Composite Solutions and RAMPF USA, this is no longer wishful thinking. Using Tailored Fiber Placement (TFP) and high-performance liquid resins, the companies are pushing the boundaries of lightweight design in aerospace, defense, transportation, medical, and green technology.
It is a well-known fact that prepreg or metallic production methods restrict design freedom with regard to shapes, for example compound curvatures or fine details. It is therefore surprising that many engineers still manufacture complex geometries and structural components using these methods.
There is, of course, a solution to this problem – carbon fiber and fiberglass composites. However, there is a snag here, too, as structural aerospace component parts are manufactured almost exclusively using prepreg-material systems or difficult-to-process Resin Transfer Molding (RTM) systems. Both approaches are established, but have their complexities and disadvantages, amongst others:
- Higher complexity is only possible using secondary assembly and bonding.
- Expensive tooling and infrastructure requirements, for example freezer storage and transport of materials, autoclave cure, heated tooling and injection infrastructure (for RTM), limited shelf life, etc.
Unlocking the full potential of composites manufacturing
“These are the main reasons why manufacturers hesitate to design composite structures and solutions, especially in the early stages of product development or for smaller-volume production, for example special mission aircraft for surveillance, aerial firefighting, and refueling, as well as helicopters and in the Urban Air Mobility market,” explains Max Schultes, Chief Technology Officer at RAMPF Composite Solutions. “The risk is too high that the required investment in tooling infrastructure increases or must be repeated, should the development cycle necessitate modifications.”
At RAMPF, the combination of cutting-edge TFP technology used by RAMPF Composite Solutions and high-performance liquid resin systems developed by RAMPF Group makes composites manufacturing more automated and less costly – including for complex geometries and structures:
- RAMPF Composite Solutions uses an eight-head TFP machine that deposits and stitches fiber materials at high speed and with maximum accuracy. The structural performance of the composite is maximized, while also providing for greatest possible weight savings, reduced carbon fiber usage, and lower cost.
- RAMPF USA has developed TFP-suitable liquid resin systems that feature low temperature-processing characteristics, for example resin infusion at 40 °C, as well as excellent wetting properties that guarantee for the effective and quick infiltration of TFP preforms. This goes together with the automation of performance-critical process steps such as mixing, degassing, and dispensing the resins. Furthermore, qualified material properties allow for an easy process transfer to new products, applications, and manufacturing sites.
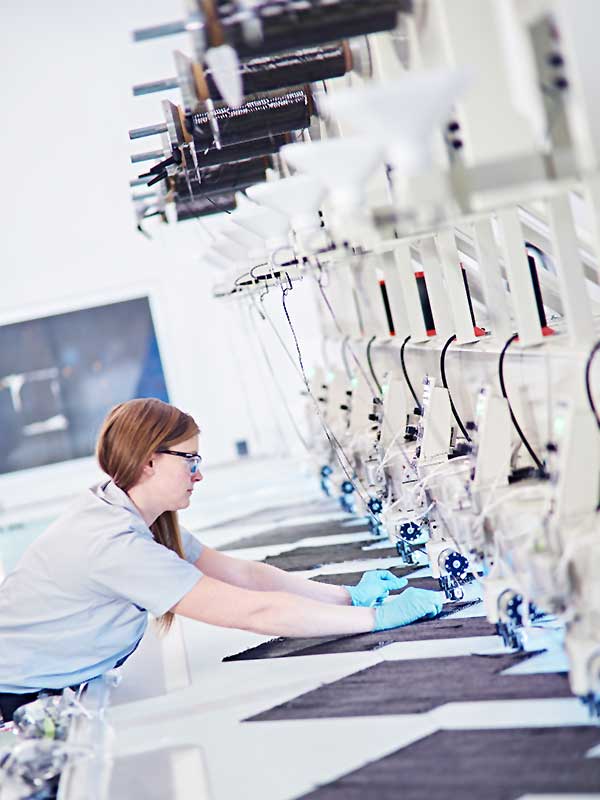
Four and a half times less weight
In a particularly impressive TFP project, RAMPF Composite Solutions transformed a stainless steel part used in commercial aircraft to a part made almost entirely of carbon fiber, resulting in the part weighing four and a half times less without an increase in costs. In fact, the customer was able to realize additional operational cost savings because of the significant weight reduction.
Furthermore, only five lay-up preforms were produced compared to the 75 that would have been required using traditional carbon composite design approaches.