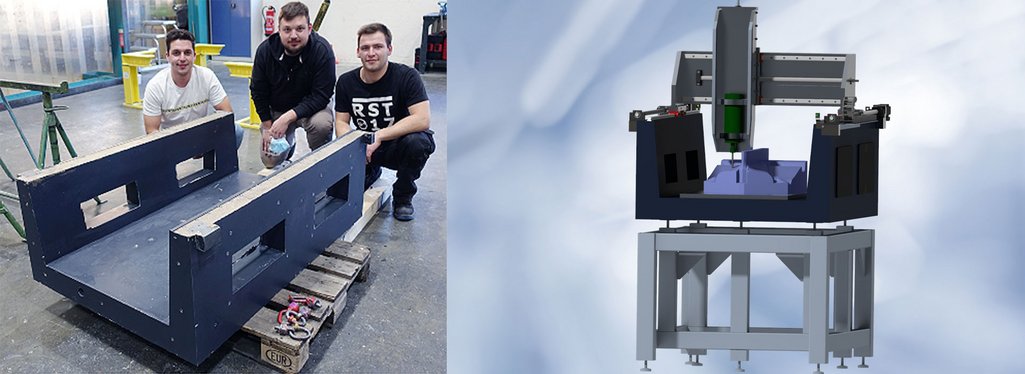
It’s Show Time at the Hockenheimring – Part 2
Fruitful exchange between university and industry – three Master students from the Esslingen University of Applied Sciences have launched the “Race to Mill” project in cooperation with RAMPF Machine Systems. They are developing a 3-axis portal-milling machine using EPUMENT® mineral casting as a vibration-damping and sustainable foundation.
RAMPF employees Rebecca Sanwald and Franziska Wasserberg were guests at Formula Student Germany (FSG) at the Hockenheimring this summer. In part one of the blog, they reported on their visit to the Esslingen University racing team and their impressions of the international event. In part two, you will now find out what the “Race to Mill” project is all about and how the team did at the "Ring".
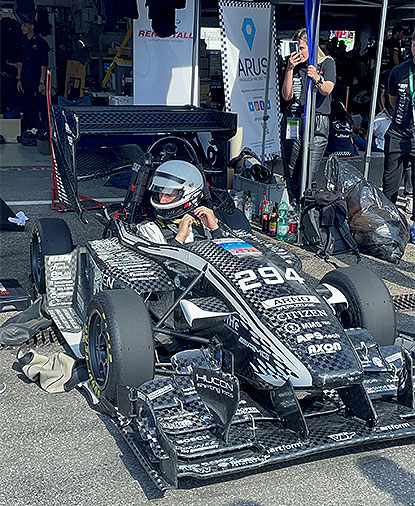
Lighter. Faster. Composites.
In racing, every tenth of a second counts. Functionality, speed, and precision are critical for success. That is why the students from the Esslingen University racing team worked for several months on the Stallardo'22, their racing car for the 2022 season, before they competed at five Formula Student events throughout Europe in the summer.
When manufacturing the car, the team used numerous carbon components. The high-tech material not only looks classy and sporty – thanks to its low weight as well as high strength and rigidity, it is predestined for use in motorsports.
“Over the years, the number of parts made of carbon for our racing cars has continued to increase. As a result, the molds required for production have also become more important,” explains Tim Ankele from the racing team of Esslingen University.
Each component is custom-made, with the students making molds from RAKU® TOOL board material from RAMPF Tooling Solutions. Due to the increasing number of carbon parts, more and more molds are required – but so far, the team has only been able to produce them on milling machines from sponsors.
One step beyond
When David Rommel, Nedeljko Alempijevic, and Tim Ankele (picture top, from left to right) initiated the “Race to Mill” project as part of their Master's course "Resource Efficiency in Mechanical Engineering", their motivation was clear – the racing team should be able to work more independently and flexibly. Supervisors of the project were Prof. Dr.-Ing. Ulrich Walter and Dipl.-Ing. (FH) Frank Hafner from Esslingen University.
The students set about constructing a 3-axis portal-milling machine that can be used in mold and model making to produce tools for hand lamination and other milled parts. The focus is on the dry processing of plastics, aluminum, and wood.
The project team developed a tailor-made technical concept – and with that, they had actually fulfilled the project specifications from the university. However, technical drawings and CAD models cannot be used for milling...
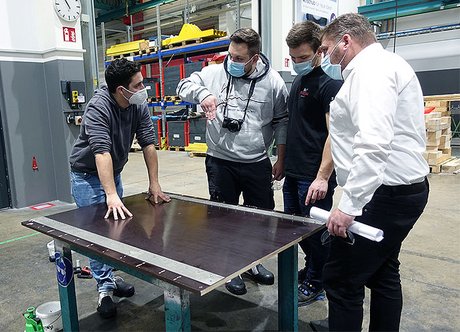
Sustainable material is a must
The focus of the "Resource Efficiency in Mechanical Engineering" course is the development of high-performance products via procedures and technologies with the lowest possible consumption of material and energy. It was therefore obvious to the Master student’s right from the start that only a sustainable material would come into question for the machine bed of the milling machine.
Due to its excellent thermal properties, outstanding damping properties, and unrivalled ecological balance, the high-tech mineral casting material EPUMENT® from RAMPF Machine Systems was the obvious material choice. In several meetings with the company’s CEO Marc Dizdarevic (picture right), the students perfected their design and developed a casting mold.
Warm welcome in Wangen and Bessenbach
Just a few months after their first inquiry, the time had come to build their self-constructed casting mold in RAMPF’s assembly hall in Wangen, where it was also filled and demolded. The students spent a total of three days at RAMPF Machine Systems and received a lot of support from the company’s engineering experts.
Before the finished machine bed could finally be brought to Esslingen, it received the finishing touches at the RAMPF Precision Grinding Center in Bessenbach.
The students are very grateful for the support the received from RAMPF:
Without the help of RAMPF’s employees we would not have been able to implement the project, as it would have already ended at the design stage.
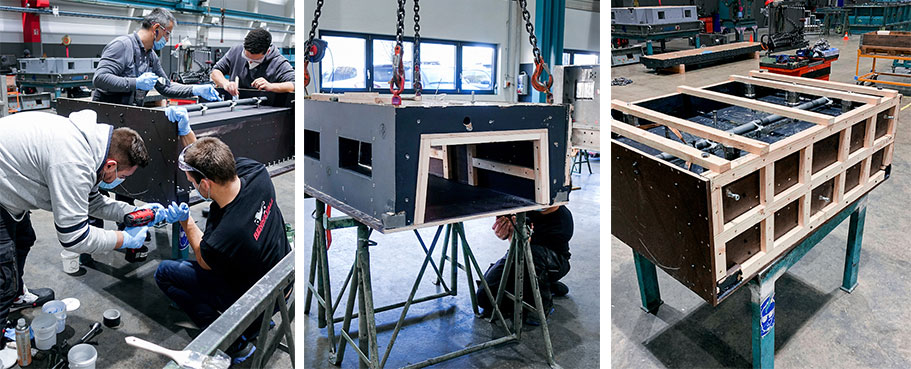
“Race to Mill” project ready for the next lap
The production of the machine bed was a significant step in the manufacture of their own milling machine. However, it will still be some time before the racing team can put it into operation. Tim, David, and Nedeljko have handed the project over to a follow-up team, which is now continuing to work on the development of the machine as part of their two-semester master's project.
The students are currently busy designing an ergonomic substructure. The frame is an essential part of the machine, without which even the most precise construction is of little use.
Prof. Dr.-Ing. Ulrich Walter, who has been involved in the project from the start and is also in charge of the current team, explains:
We want the machines designed by our students to be very precise and meet high standards.
Once the substructure is finished, only the axles and slides on the milling machine have to be added to complete the “Race to Mill” project – and then the machine can be used by the racing team to manufacture their own composite parts.
Bad luck at the „Ring“, resounding success in Croatia
So how did the racing team from Esslingen fare at this year’s event at the Hockenheimring?
Tim Ankele reports:
At the FSG, a cable frayed during the endurance race and there was a short circuit, so that many components no longer received any power. That was quite annoying because we did really well in the other disciplines and had good chances of winning the event. At the last round in Croatia, we won the endurance, autocross, skid pad, engineering design, and cost-report disciplines and, in the end, the entire event. We even set an unofficial world record in the skid pad.
RAMPF CONGRATULATES THE RACING TEAM FROM ESSLINGEN ON A SUCCESSFUL SEASON, ESPECIALLY THE victory AT THE event IN croatia! WE WISH THE STUDENTS ALL THE BEST FOR THE FUTURE!
Close cooperation of RAMPF & Universities
The companies of the RAMPF Group place great importance to the exchange with academic institutions. On the one hand, this inspires and accelerates the innovation process and leads to the development of new products and solutions. On the other, it enables students to apply their knowledge in practice and to prepare for future specialist tasks. In addition, contacts are made and effective networks established between industry and universities. RAMPF offers work student and internship positions as well as theses.
> A partnership with the Faculty of Applied Chemistry and Technology has existed with Reutlingen University, Germany, since 2015. This encompasses, among other things, joint events such as specialist lectures and company visits. RAMPF regularly welcomes Reutlingen students to do internships, become a working student, and write dissertations. It also enables them to directly start working at the company.
> RAMPF has been working with Steinbeis University (School of International Business and Entrepreneurship) in Herrenberg, Germany, since January 2021. As part of this partnership, the dual degree programs “Digital Leadership” and “International Management” are offered.
> Initial talks a future cooperation have already taken place with the Faculty of Natural Sciences, Department of Chemistry, at the University of Ulm. A working student from Ulm is currently at RAMPF, who previously got to know the company as part of an internship.
> RAMPF works together with the DHBW Stuttgart in the dual study courses Business Administration and Mechatronics & Mechanical Engineering.