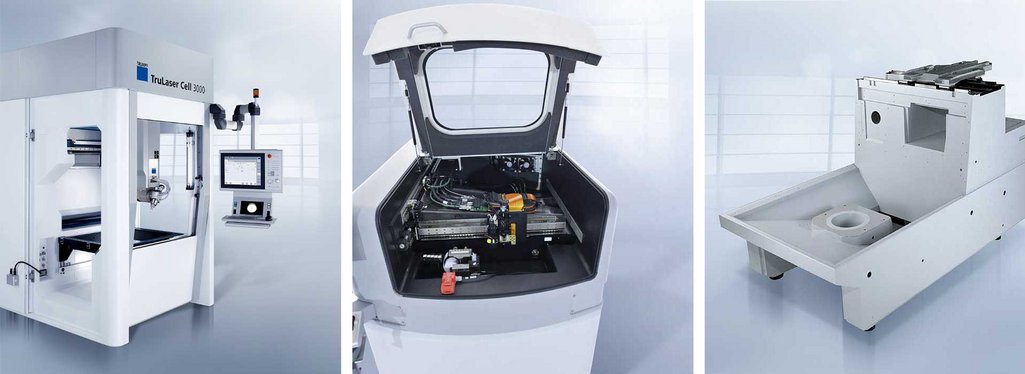
Mineral Casting for industrial applications – Part 1
Since the end of the 1990s, alternative machine bed materials such as EPUMENT® mineral casting and EPUDUR ultra-high performance concrete have become increasingly important in mechanical engineering and dynamic production technology. We will explain in the following why this trend can also be observed in the machine tool engineering, electronics manufacturing, and laser industries.
There are a multitude of reasons for the growing popularity of alternative machine bed materials:
- Unbeatable vibration damping
- Outstanding thermal stability
- High degree of functional integration
- Maximum design freedom
- Optimum static and dynamic rigidity
- Competitive costs
- Exceptional ecological credentials
- Very short procurement times with mold in place (time to market)
In conventional machine tool engineering, there is a rising demand for completely pre-assembled basic machines, as more customers look to focus on their core areas of expertise and pass on other work to external specialists. The goal is for companies to keep the throughput times in their own assembly facilities as short as possible. However, the entire unit comprising a machine bed and linear, drive, and control technology is usually developed and designed in-house, as this plays a key role in the process.
Things are a little bit different in the semi-conductor and laser industries. Innovative processes are developed here, meaning conventional mechanical engineering is not the focus. For these industries, it is extremely important to have a partner who is well versed in all disciplines – from designing machine beds and linear and drive technology all the way to wiring machinery.
Kacper Lasetzki, Sales Manager at RAMPF Machine Systems:
At one time, mechanical engineers would develop their own linear, drive, and control technology. However, new and extremely dynamic processes are constantly coming into play in this highly innovative sector, and these need to be re-flected in the machinery. As a result, the drive and guide components, not to mention the machine bed, are subject to the most stringent requirements. We were quick to pick up on that – and this competitive edge not only works to our benefit, but naturally also to that of our customers.
In Part 1 of our two-part blog post, we show you why leading companies in the machine tool engineering, electronics manufacturing and laser industries place their trust in RAMPF Machine Systems.
Machine tools
When it comes to using alternative materials for machine beds, machine tool manufacturers are true pioneers. They have been successfully using EPUMENT® mineral casting beds and gantries and steel composite structures filled with EPUFILL mineral casting since the 1970s.
Besides load-bearing and damping functions, machine beds made of ultra-high performance concrete (UHPC) from RAMPF’s EPUDUR brand also perform design and chip management tasks in machine tools. Filled steel composite structures are the state of the art for large-volume and heavy beds in machine tools, for example machining centers for machine tool and mold making, which are required in small quantities.
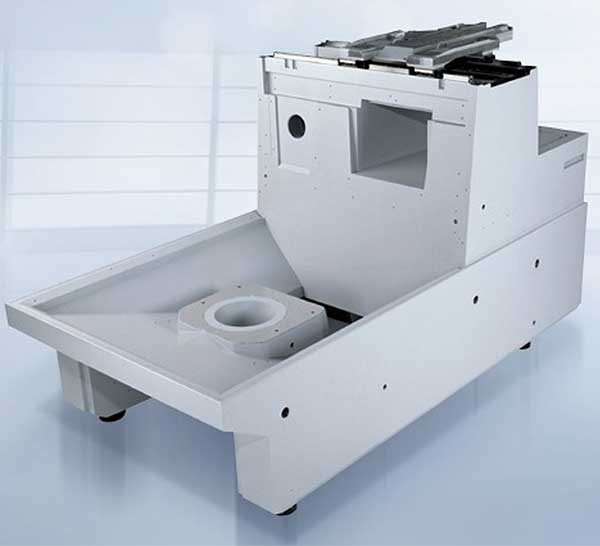
Electronics manufacturing
The number of applications for alternative machine bed materials in machinery and equipment for electronics manufacturing has also increased dramatically. Processes in the industry such as bonding, jetting, dispensing, placing, assembling, and packaging are characterized by exceptional dynamics and require maximum precision. For example, jet print technology, which has supplanted conventional screen printing throughout the world, needs to handle accelerations up to 4 g while also delivering total print accuracy. The jet printer shown achieves this with a mineral casting machine bed and an extremely lightweight carriage made of carbon-fiber-reinforced plastic.
Wire and chip bonding are highly dynamic processes for manufacturing integrated circuits. Placing over 30 soldering points a second increases mechanical resonance and agitates the entire machine structure more. This is another application where damping materials have become a popular choice for machine bed components.
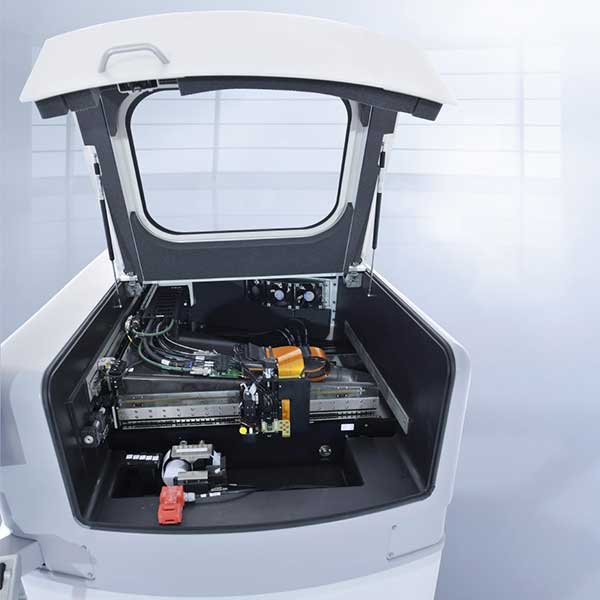
Laser applications
Lasers have become a virtually universal tool in modern production technology. Laser cutting, welding, marking, coating, scoring, and many other processes play a key role in such technologies. Laser applications therefore offer a wide array of uses for alternative materials in machine beds and machine bed components.
In 5-axis laser machining centers, which can be used for two- or three-dimensional cutting and welding, a multi-functional mineral casting bed supports exceptionally dynamic processes and ensures the necessary vibration damping. Key features of this end-to-end solution are high-precision assembly surfaces for profile guide rails manufactured using non-cutting processes, design- and function-oriented visible surfaces, and integrated media routing.
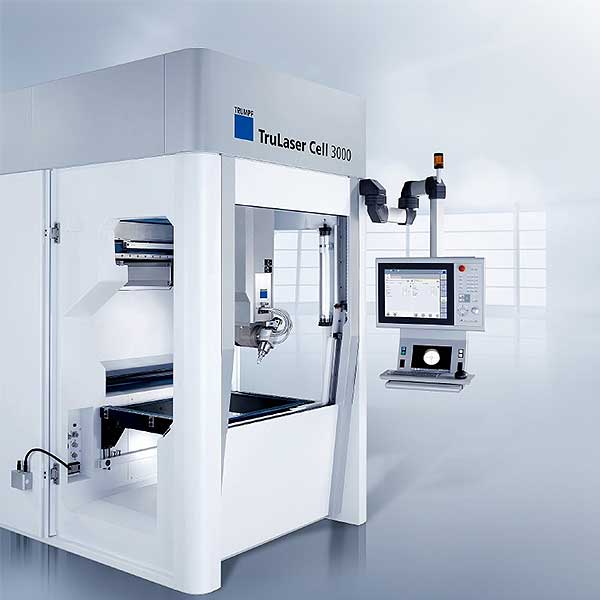
IN PART 2 OF “MINERAL CASTING FOR INDUSTRIAL APPLICATIONS”, YOU WILL DISCOVER WHY ALTERNATIVE MATERIALS HAVE ALSO BECOME A POPULAR CHOICE FOR SOLAR MODULE PRODUCTION, WOODWORKING AND TEXTILE MACHINERY, MEASURING, TESTING, AND INSPECTION TECHNOLOGY, AS WELL AS MACHINERY USED IN ENERGY TECHNOLOGY, AND SPECIAL MACHINES.