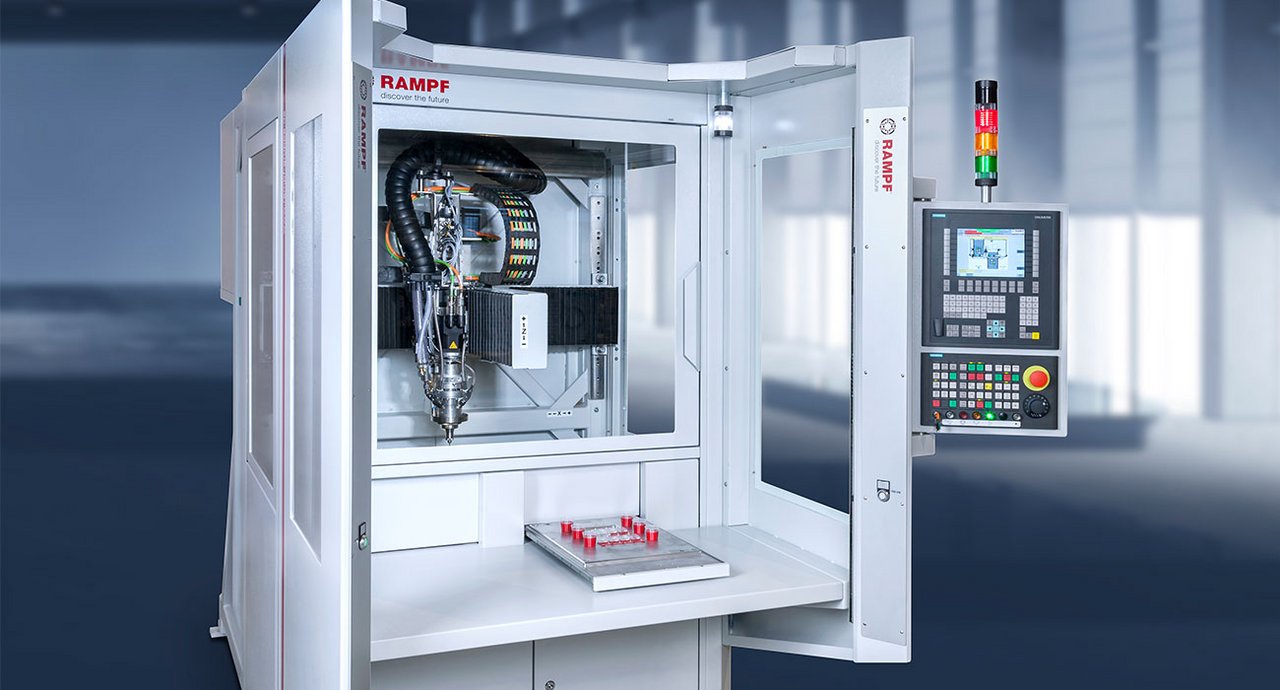
Compact dispensing cell DC-CNC800 combines flexibility and dynamics
Compact, flexible, high-performance: DC-CNC800
Featuring an integrated material preparation system, the DC-CNC800 can be fitted with piston or gear pumps. For modular control, a CNC Siemens Sinumerik control system and Beckhoff control technology are available. A further advantage: integrated process control for continuous monitoring of pressure, fill level, and speed.
The DC-CNC800 can be optionally equipped with a high-pressure rinse agent recycling and water-rinsing system, numerous other automated equipment components, and the MS-C mixing system for dispensing rates of 0.1 g/sec and higher.
Further features: standardized operating concepts for sliding tables, rotary index plates, and conveyor feeds as well as the integration of vacuum barrel presses. Large tanks enable small containers to be fully filled in a single step, and access for maintenance work on the piston and gear pumps as well as controls is easy.
Visitors to Bondexpo can see the DC-CNC800 in action at the RAMPF booth in hall 6 / booth 6404, where the system will process a casting application.
ERROR: Content Element with uid "42246" and type "textBesideImage" has no rendering definition!
Optical Bonding – Vacuum application for best results
At Bondexpo 2018, RAMPF Production System is also presenting its fully automated joining method for the bubble-free application of bonding materials for displays in the automotive, mobile devices, GPS, industrial monitors, navigation, and wearables markets.
In the Optical Bonding process, the display and touch glass/cover glass are placed on top of each other. The air in between is excluded with the help of an extremely clear bonding compound. This avoids parallax errors, which are caused by the different refractive indices of air and glass and affect the viewer by blurring and an impaired side visibility. Since the bonding compound has approximately the same refractive index as glass, the result is a significantly sharper image and much improved side visibility.
The bonding material is applied in a vacuum and the components are joined in an airless environment. The thin-film degassing technology of the single components makes it possible to process highly degassed bonding material. This minimizes the risk of air bubbles being trapped during the joining and curing processes.
The bonding material is dispensed by the RAMPF DC-VAC Vacuum Dispensing System. Designed for processing one- and two-component casting materials, the cell is equipped with material conditioning under vacuum and the dynamic mixing system MS-C. The DC-VAC combines C-DS gluing units, assembly units, robot systems, conveyor systems, and process control systems to a fully automated, customized production system.
In addition to the display joining method in a vacuum, RAMPF’s fully automated production system also features all the operations for handling, aligning, and bonding the displays to frames as well as final quality control.
ERROR: Content Element with uid "42248" and type "textBesideImage" has no rendering definition!