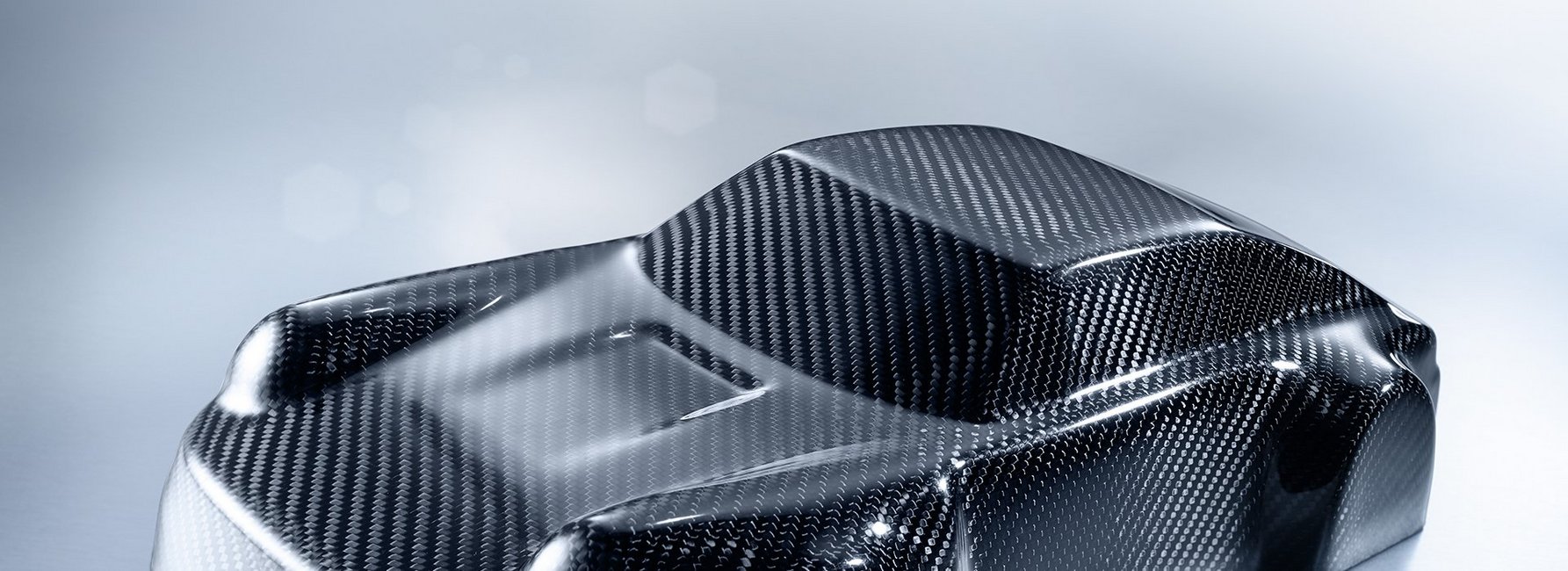
Epoxy & Polyurethane
Liquid Systems
Best Results guaranteed.
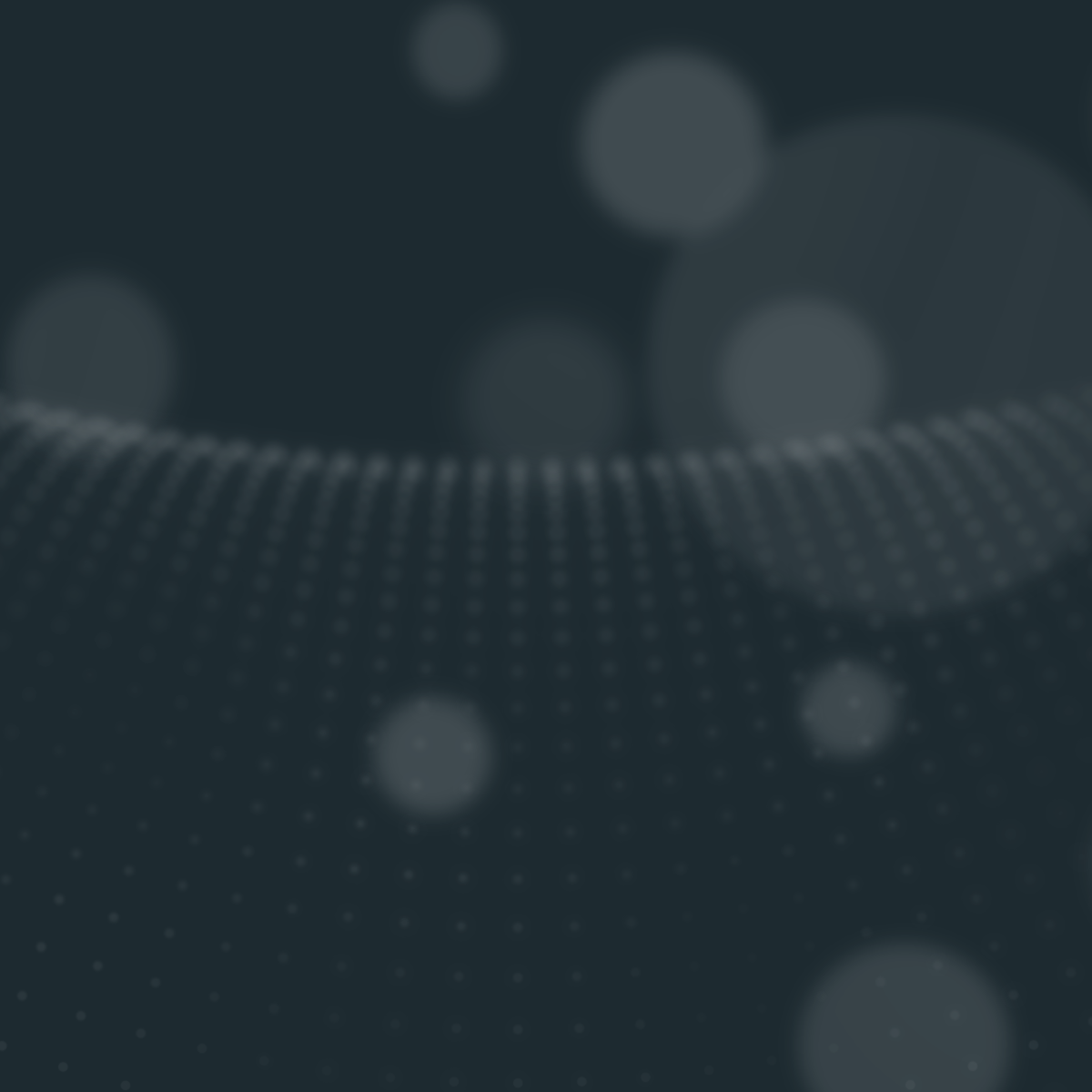
The RAKU® TOOL coupling coat is a prefabricated two-component epoxy system. It ensures a good adhesion of the gelcoat to the backing and is applied with a brush in a thin, uniform layer.
Depending on the operating conditions, the backing can be made from casting resin, tamping, fiber laminate or laminating paste.
RAKU® TOOL laminating resins produce lightweight, rigid, and – depending on the type of fiber – high-strength molds and parts with or without gelcoat.
The portfolio includes solvent-free two-component epoxy systems with wide-ranging pot lives and degrees of temperature resistance for processing glass, carbon, and aramid fibers among others.
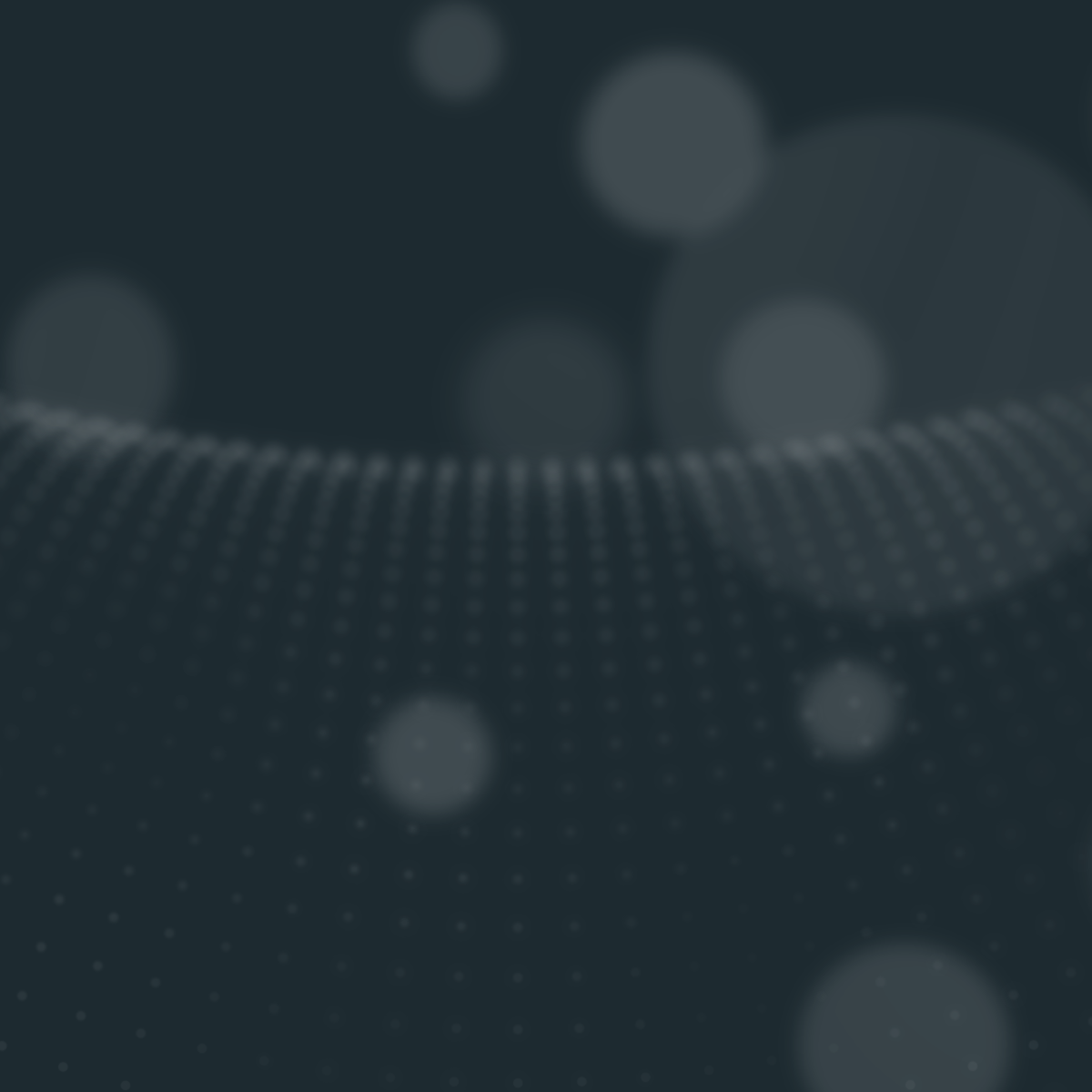
RAKU® TOOL laminating pastes are used to reinforce molds and tooling aids, and also to make laminated shells, jigs, and fixtures.
The manufacturing process is very fast compared to the laminate build-up method, as the required shell coating thickness (up to 15 mm) can be applied in a single process.
RAKU® TOOL infusion systems ensure optimum impregnation of dry fiber packages under pressure and in a vacuum.
A wide range of high-strength, solvent-free two-component epoxy systems with medium to high temperature resistance, excellent wetting, flow, and processing properties, and long pot lives are available.
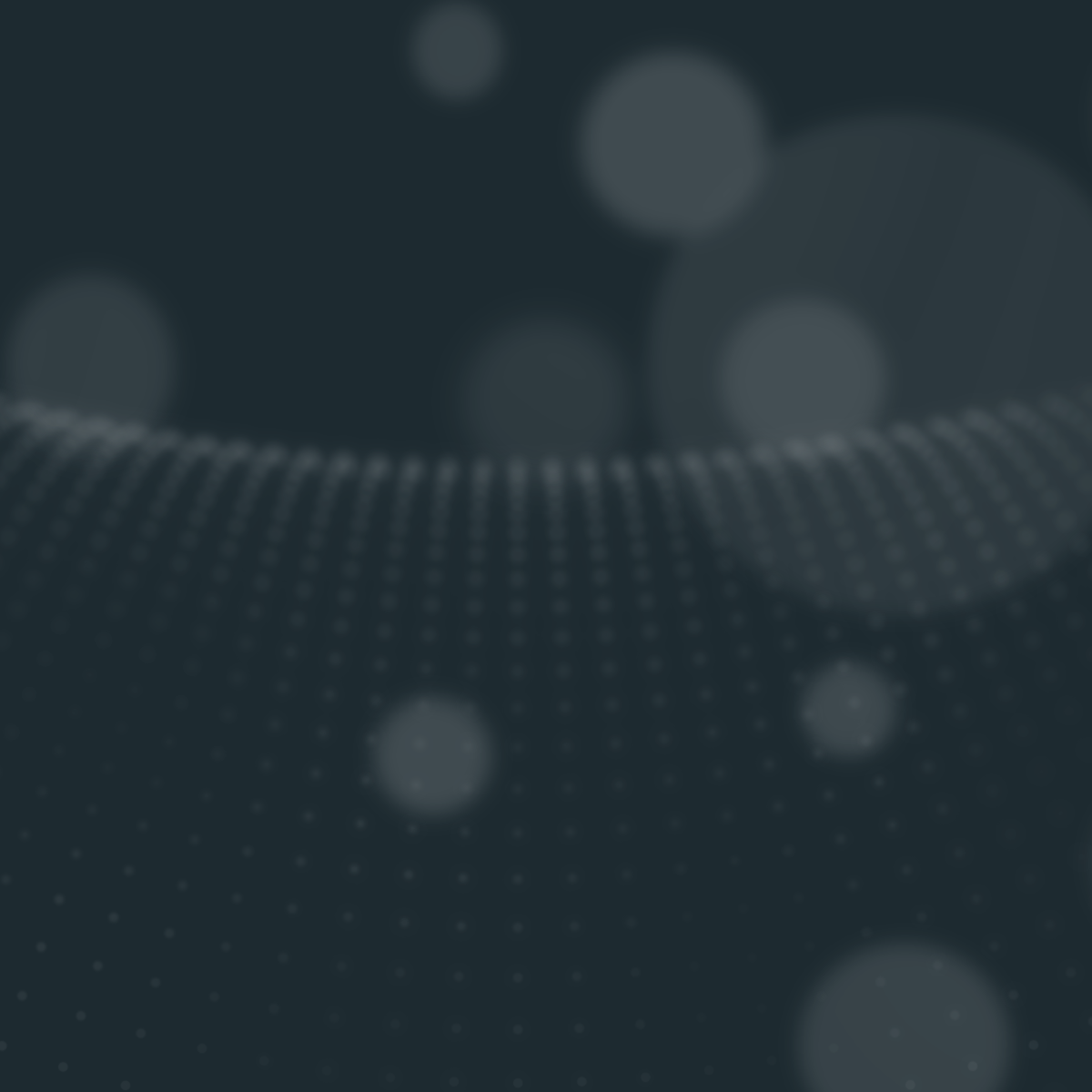
New: Cold cast elastomer Shore A55 for sanitary ceramics
- Filled, easy to cast
- Minimal shrinkage
- Optimized surface hardening in wet plaster
- Very accurate reproduction of finest patterns and details
- Structural molds for formwork, concrete molds
- Plastic molds for the ceramics industry, e.g. wash basin, sinks
The RAKU® TOOL range of casting resins for both full and face casting includes epoxy, polyurethane, and polyurea systems.
These systems are available with varying degrees of temperature resistance and different pot lives. The latter can be adapted in some cases based on the hardener selected.
The resins have a number of impressive features, including good processing and venting properties, excellent resistance to chemicals, high resistance to abrasion, and a hard surface.
RAKU® TOOL casting resins are used for modeling in general and to make items such as foundry patterns and copy models, jigs and fixtures, and working models for the ceramics industry.
Full casting - the benefits: quick and easy work process, with no need for a gelcoat. It is suitable for smaller as well as larger castings.
Face casting – the benefits: a smaller amount of casting material is required, superior dimensional stability of the casting due to lower shrinkage, and special surface properties can be achieved (from flexible to hard). Face casting is suitable for large castings.
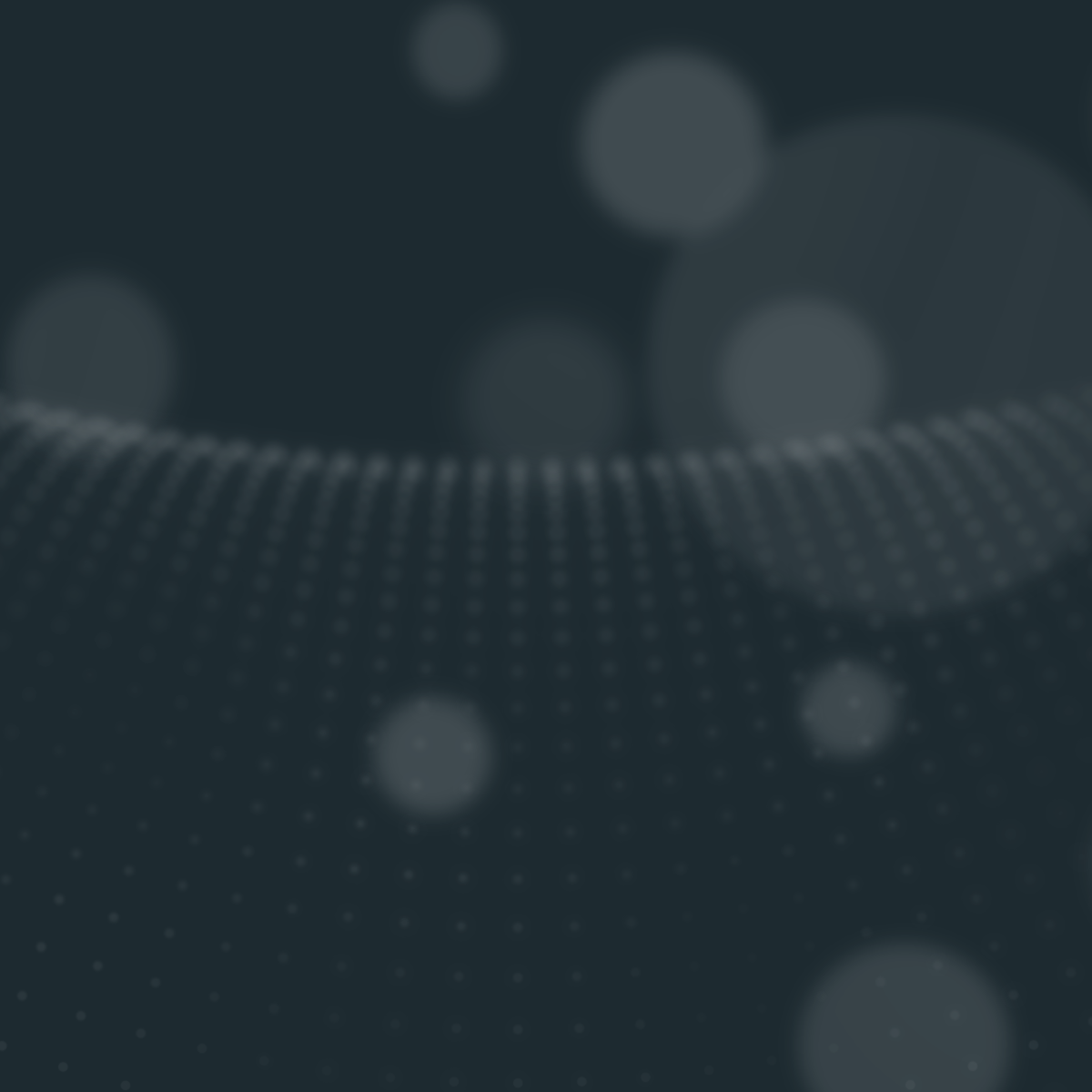
The range of RAKU® TOOL fast cast resins consists of two-component polyurethane systems that are used either filled or unfilled and can thus be cast in thin or thicker layers with various pot lives.
The resins are easy to mix and used to produce foundry models, core boxes, negatives, pattern plates, checking casts, copy models, vacuum forming molds, and jigs for trimming prototype parts.
RAKU® TOOL rapid prototyping systems make manufacturing high-quality functional prototype parts and small series both quick and easy.
The portfolio includes a wide selection of two-component polyurethane systems that are fast to demold and simulate a large number of materials such as PP, PE, ABS, and rubber.
RAKU® TOOL rapid prototyping systems offer excellent value for money during product development thanks to their shorter time to market, quick and easy imitation of thermoplastics such as polyethylene (PE), polypropylene (PP), and acrylonitrile-butadiene-styrene (ABS), prevention of development and design errors, and longer product cycles, as improvements and modifications are possible at any stage of the process.
Applications include visual models, design studies, form and suitability tests, simulation of series materials, and functionality tests.