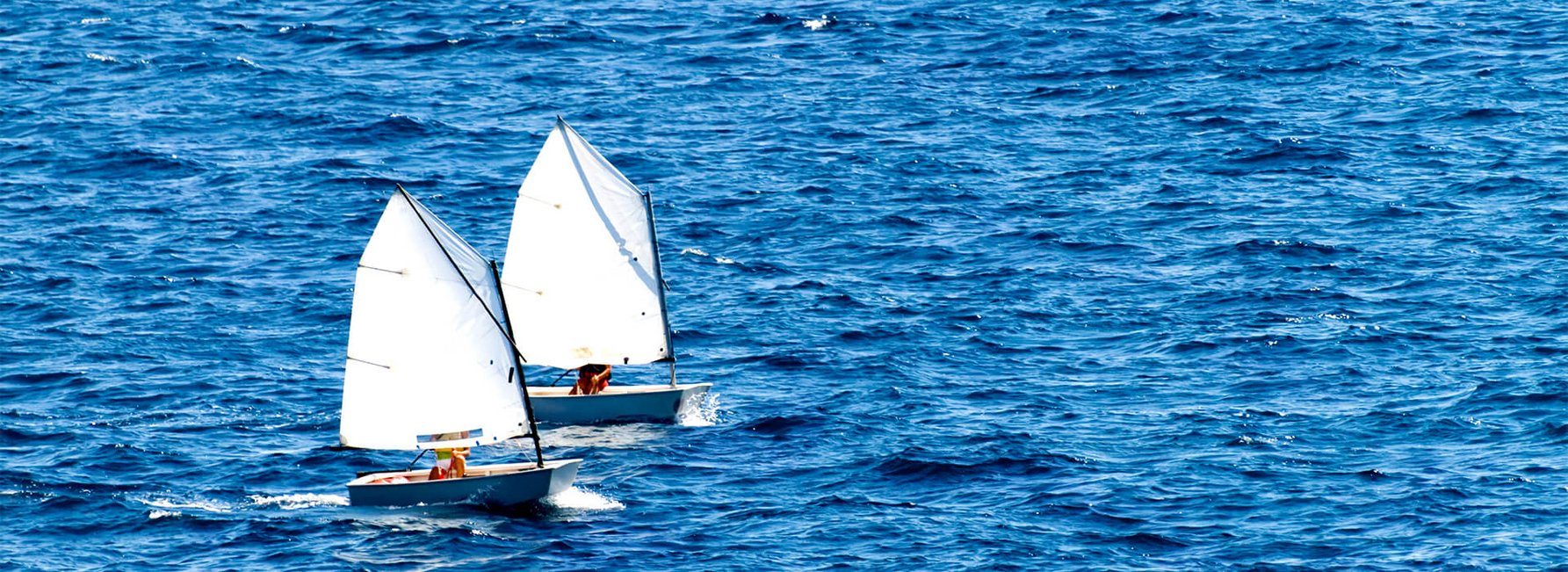
Ahoy!
Sailing fun with RAKU® TOOL MB-0600!
Set sail for a greener future!
Powered by the wind, made from natural and recycled materials: According to the manufacturer, the Eco_Optimist children’s sailing boat has an 85 percent lower CO2 footprint than conventional FRP boats and is also completely recyclable.
As a company founded on sustainability, we are proud to contribute to this exemplary product. Our RAKU® TOOL MB-0600 board is used to produce a negative mold for the deck and center bulkhead of the boat.
The high-performance polyurethane board features excellent machinability, edge stability, and finest surface quality. It is also eco-friendly – RAKU® TOOL MB-0600 is produced using a high proportion of recycled polyol.
For us, sustainability is not a burden. Rather, it is a task to which we devote ourselves with enthusiasm and dedication. That is why we are constantly developing more sustainable materials and reducing resource consumption, emissions, and production waste.
Application
Production of the negative mold for the deck and center bulkhead of an "Eco_Optimist" (children's sailing boat).
The end customer wants to build the world's first sustainable series boat and introduce the topic of sustainability to young sailing enthusiasts. The "Eco-Optimists" are made of NRP (natural fiber reinforced plastic) and therefore have a very good climate balance compared to conventional FRP.
MB-0600 board requirements:
- Excellent machinability and edge stability.
- Good demoldability – 30-50 impressions for the first series.
- Outstanding adhesion with RAKU® TOOL EP-2306 / EH-2904-1 – specially matched to the density of the board material. Highest surface quality after milling and grinding.
- Acceptable final mold weight.
- Good repairability (was proven immediately after the cutter collided with the board; the result after bonding and filling was excellent – as if nothing had ever happened).
- Good surface finish after coating with epoxy resin primer and sanding.
Production Process
1. In order to minimize waste and milling time, the blanks were drawn and optimized in CAD beforehand. The boards were then ordered precisely from RAMPF and quickly delivered.
2. The board material was cut and bonded according to the drawing.
3. The molds with somewhat complex geometries were then milled using a 5-axis milling machine.
4. After CNC milling, the molds were sanded, coated with epoxy resin primer, and sanded again – until the desired surface finish was achieved.
5. The finished molds were delivered to the customer to build the first prototypes.